The distance from the ring gear to the pinion gear is set by shims between the cover and the bearing. Often the hub with the bearing is pressed on to the cover, making adjustments with different shims difficult.
For this reason, the tubular holder in the cover is made for a perfect fit without the need for a press. Very careful sanding with a fine grid paper will get a transition fit.
The pinion gear will always push out the ring gear towards the cover. Along with the o-ring in the drive shaft, additional push is provided to keep everything in place.
The gear compound at the top of the shaft is to check for any contact with the hub. Often a common source for noise.
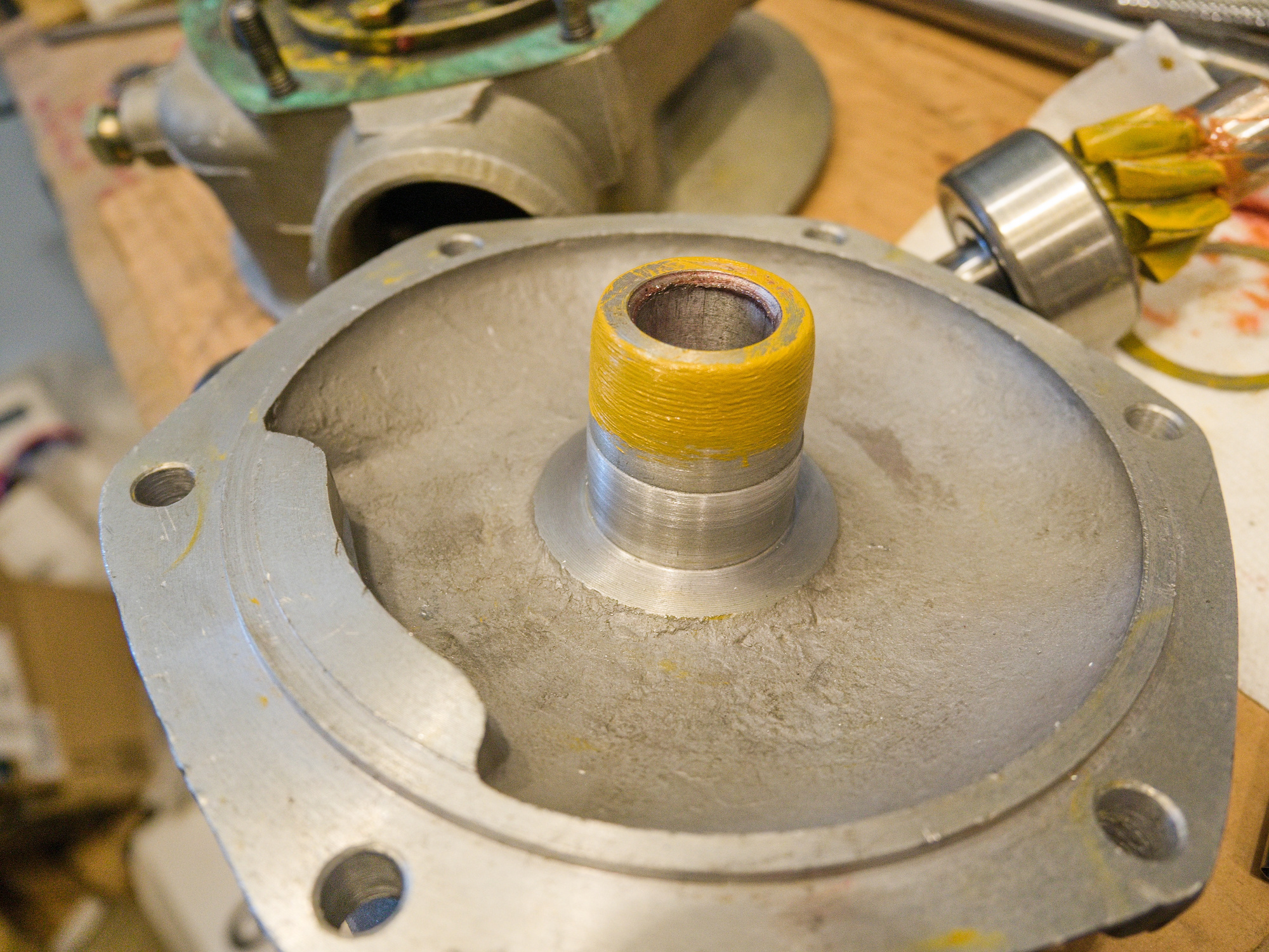
The 1-3/8"x1-7/8" Arbor Shims are used to space the ring gear. The M52x42x0.2 shims are used to space the pinion gear. The M52 shims were sold in a pack of 125 only.
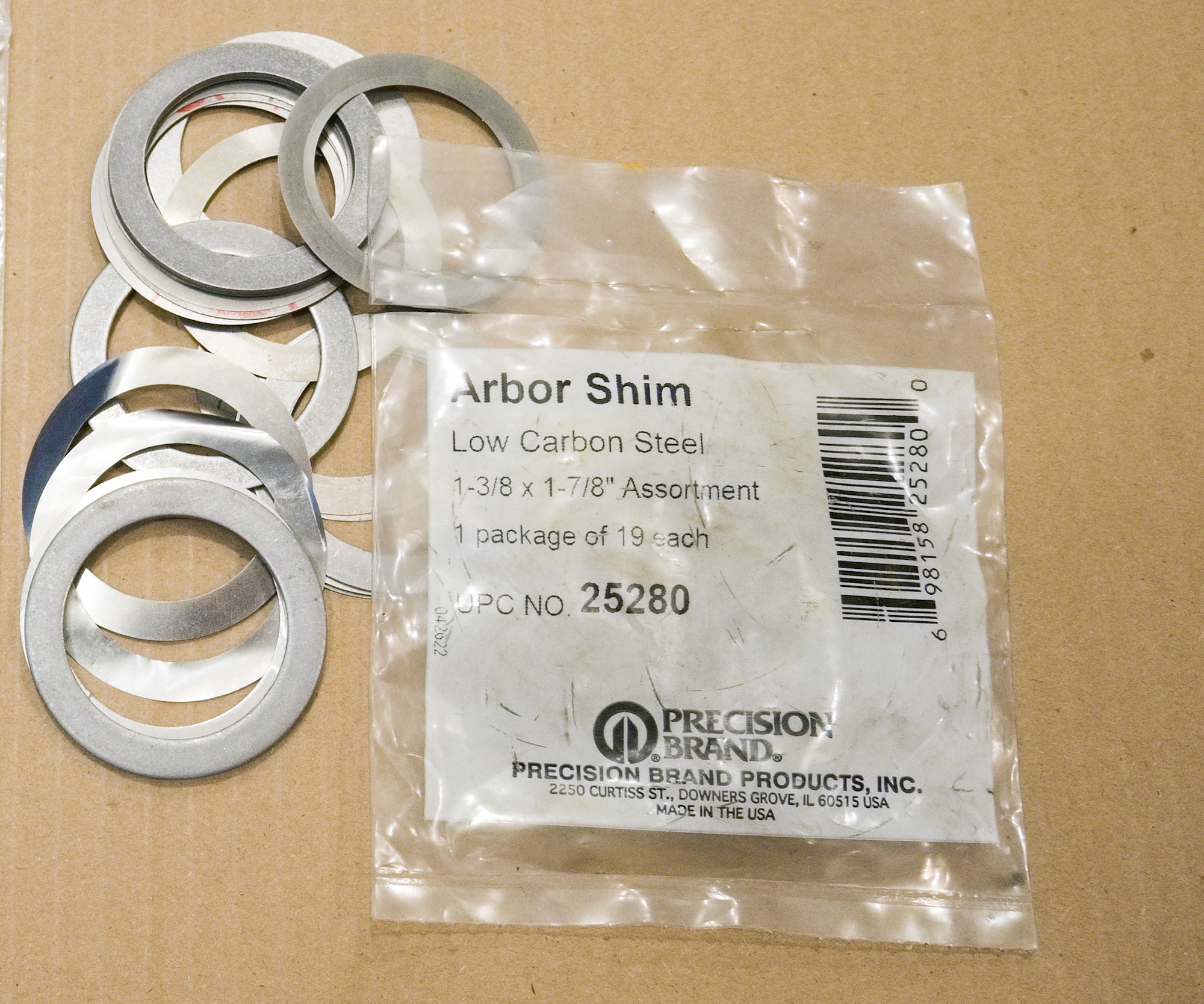
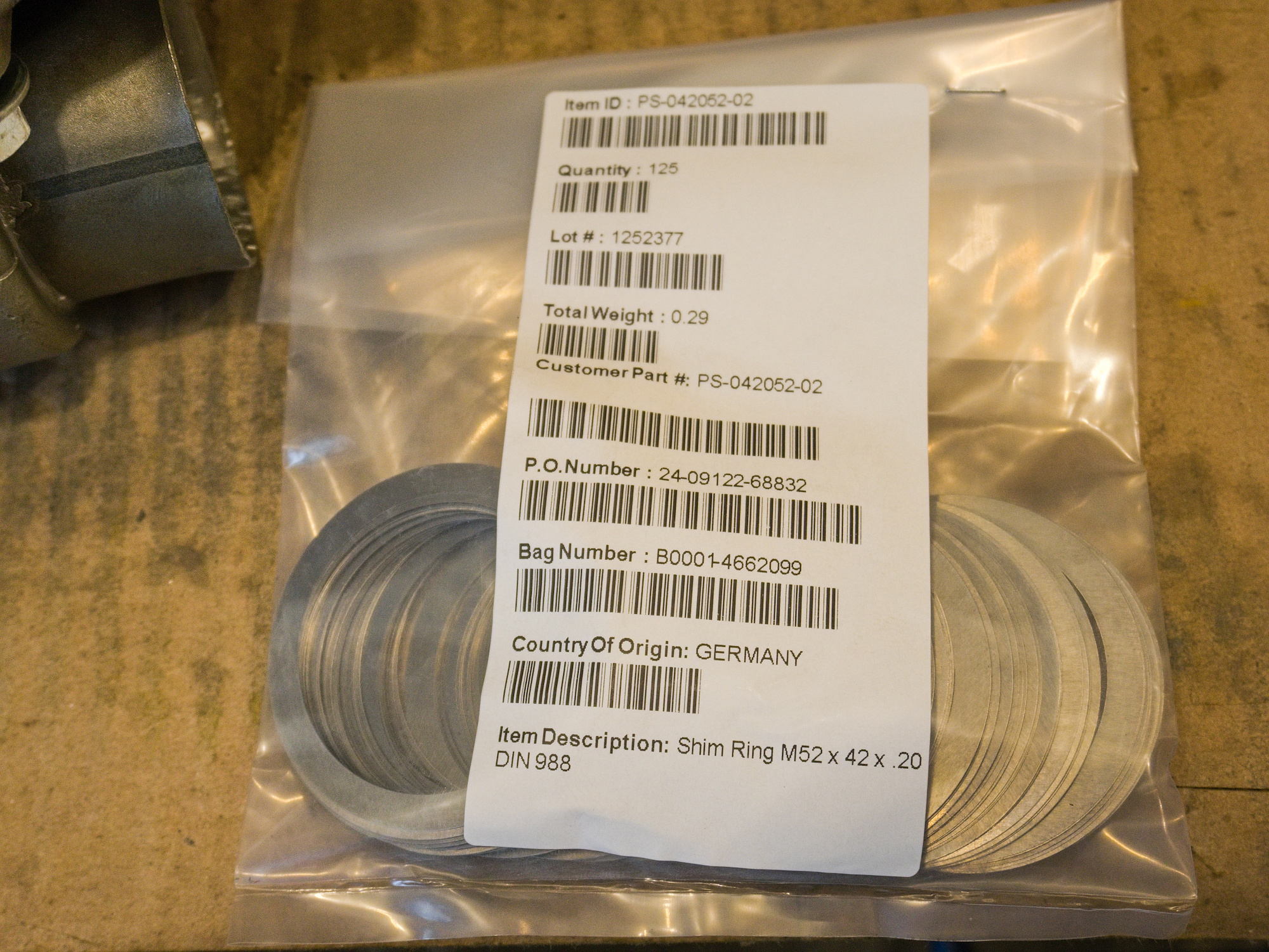
To make the pinion adjustment easier, a plastic replacement for the bearing with a undersize is used to allow quickly sliding the pinion gear in and out.

Gear compound is used to see the contact pattern.
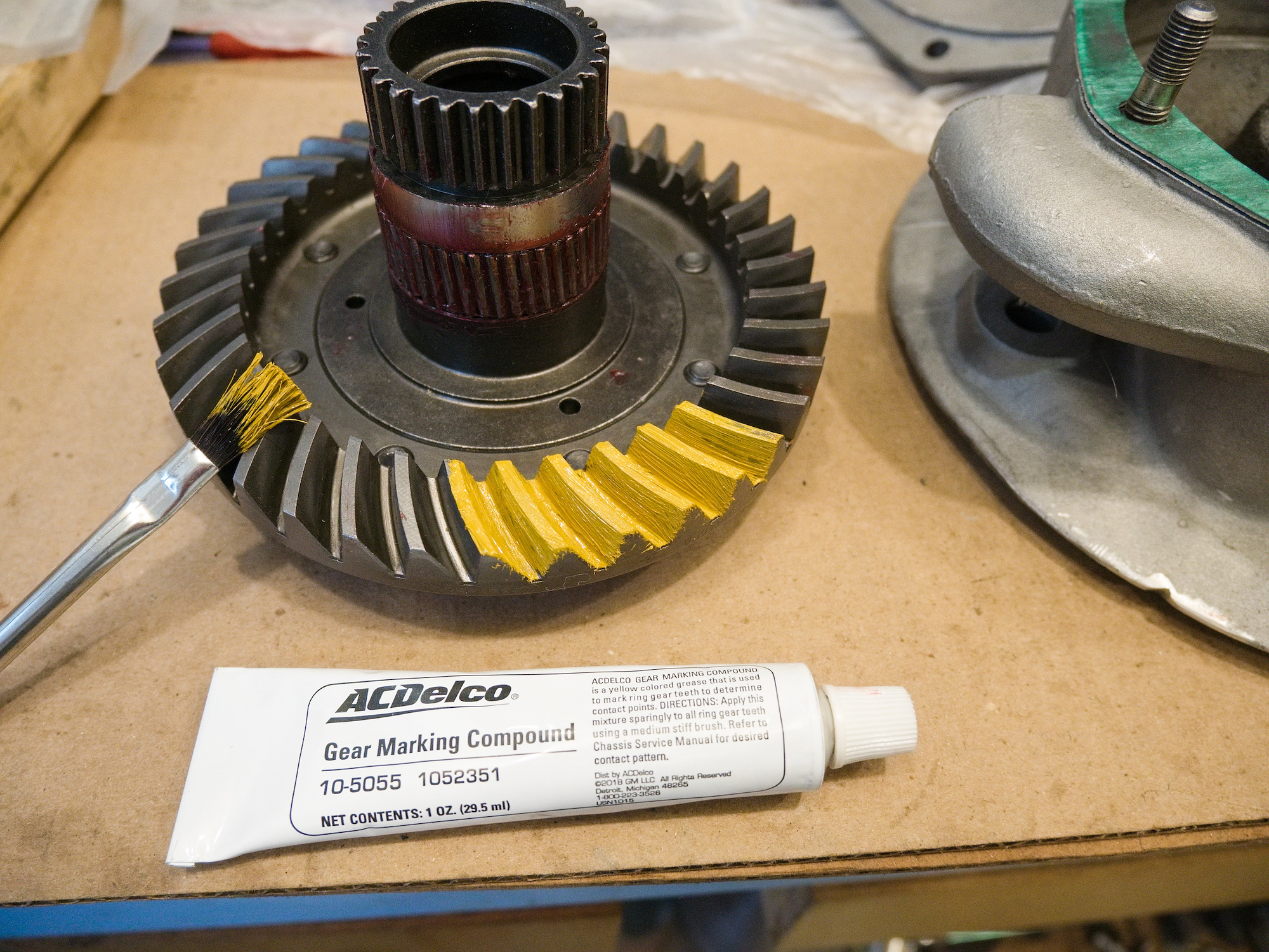
The contact pattern gets visible once the gear is rotated. Apply some pressure to the ring gear when rotating the pinion gear to get a clear pattern.

Rotate forth and back to get a pattern for the cruise and drive side.
This is the drive side. Needs adjustment.

This is the cruise side. Also not acceptable. The distinctive bottom line must not appear. The pattern should be uniform and gradually fade out.

Guide to adjust the contact pattern.
Search for contact pattern to get more detailled guides on how to adjust the gears.
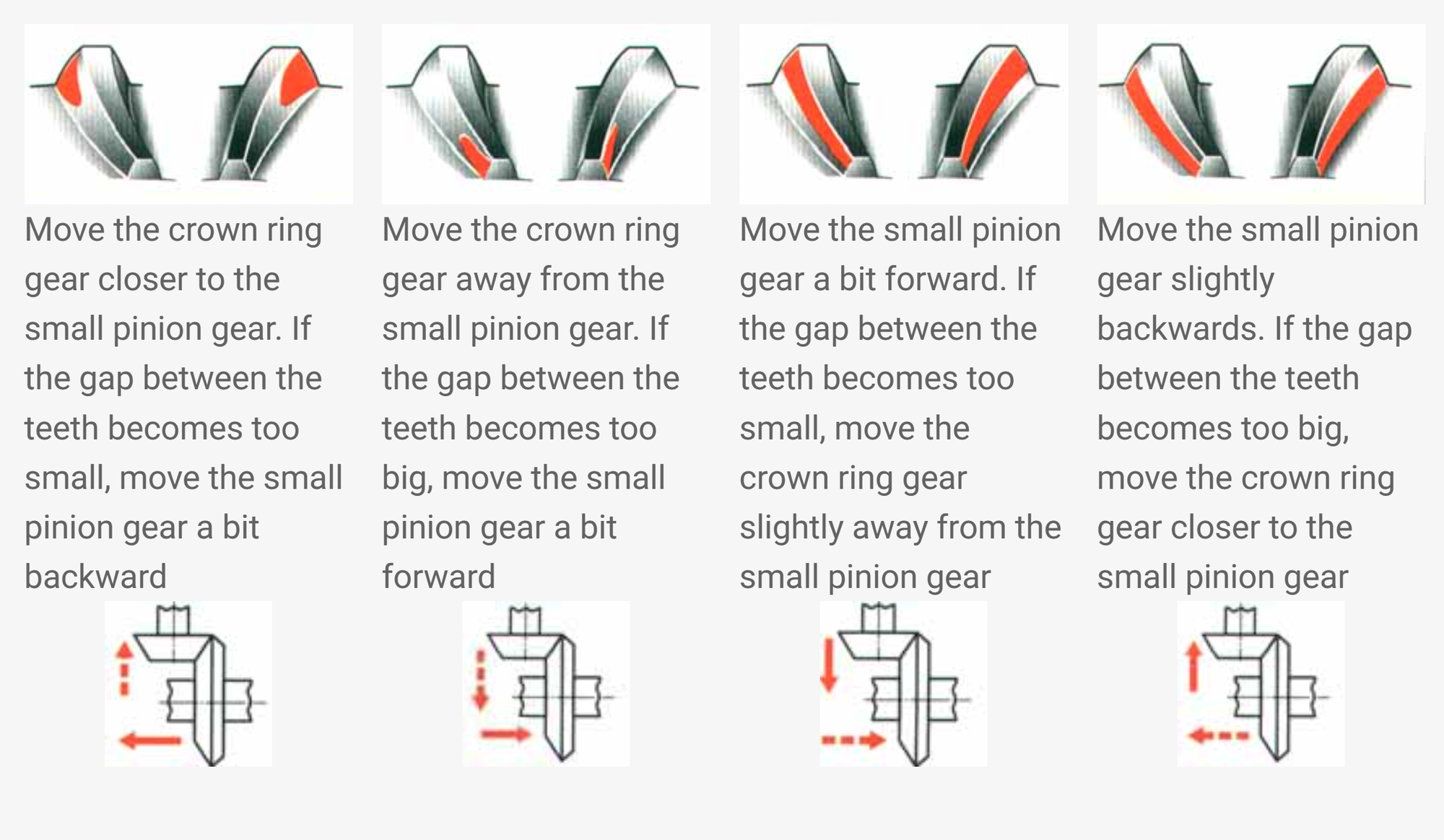
Using the contact pattern guides, move the ring gear by adding or removing 1-3/8"x1-7/8" Arbor shims between the cover and the hub bearing, and move the pinion gear by adding or removing M52x42x0.2 shims between the housing and the bearing.
Acceptable contact pattern for the drive side.

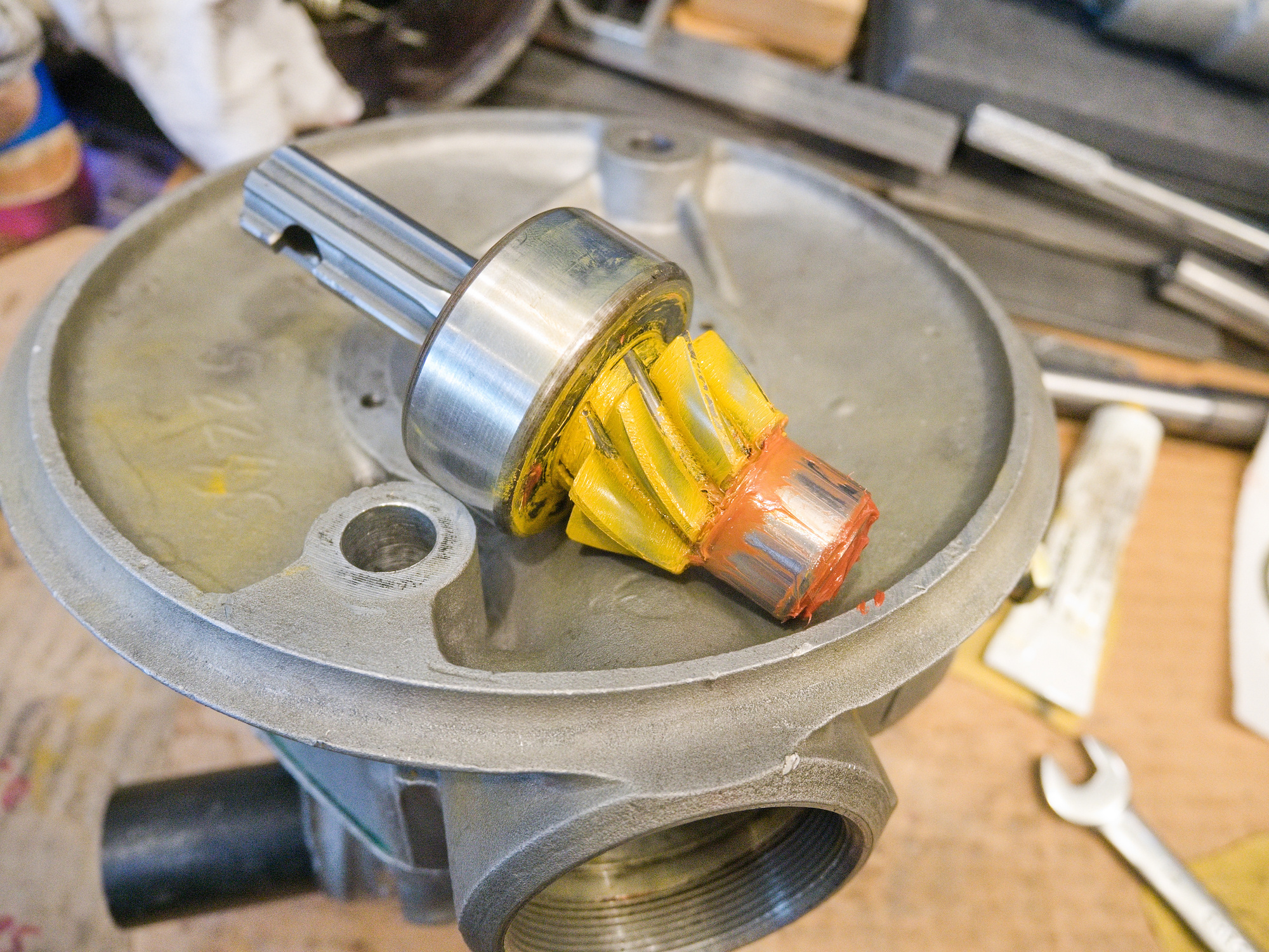
The distance bushing is made out of 1"x0.12"x0.76" DOM Mild Steel Tube A513 and drilled to an internal diameter of 20mm on the lathe. The old one was rather sloppy and was not perfectly even.
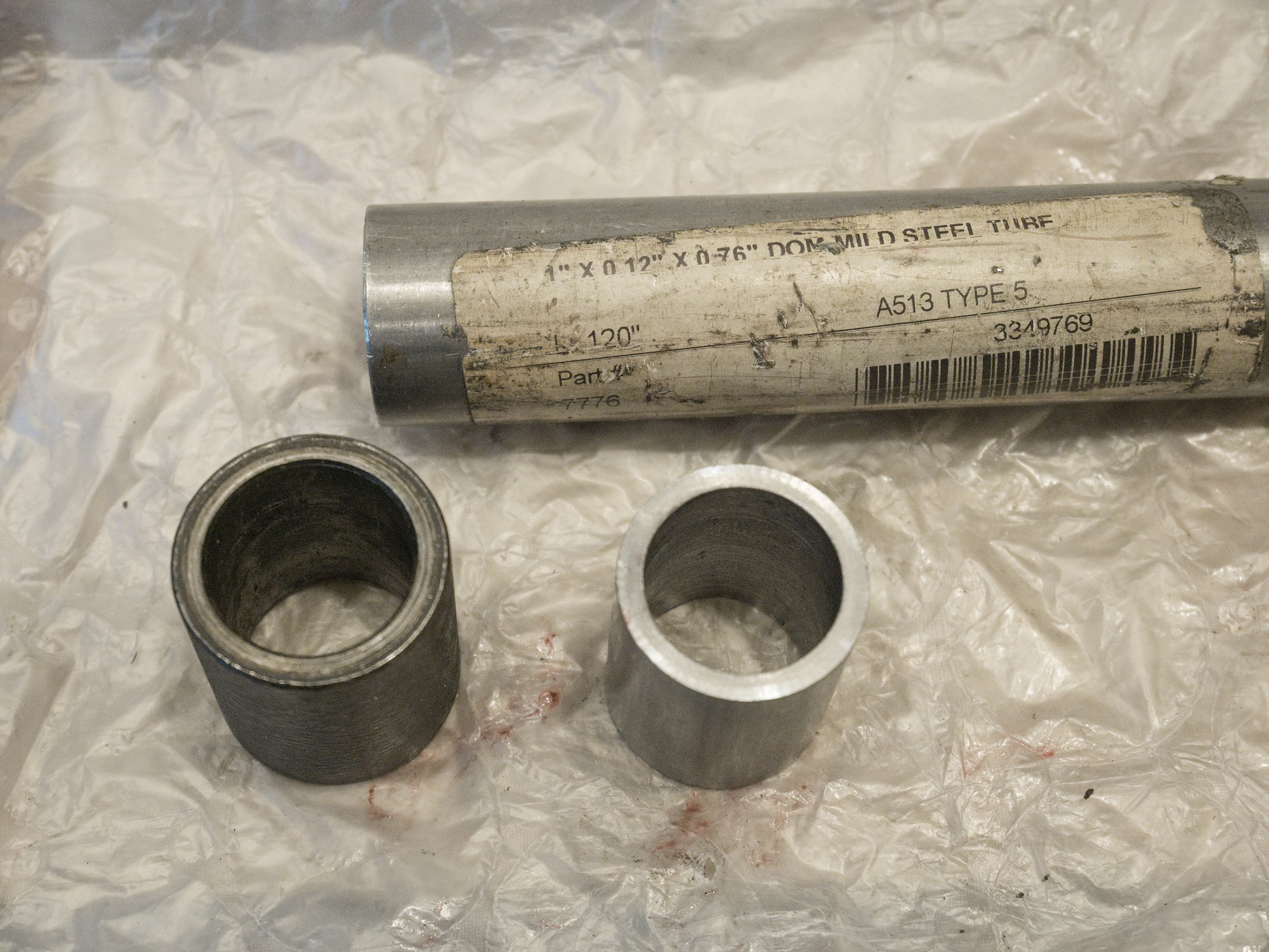
Check the distance and the seating of the driving gear. I have put a large o-ring inside the wheel hub to push the hub towards the cover. This ensures the ring gear always seats against the cover and maintains proper distance of the gears.
The CJ750 FD does not use the bronze slitted washer to keep a minimal distance between the ring and pinion gear, and with the o-ring on the wheel side, the ring gear never slides towards the pinion.
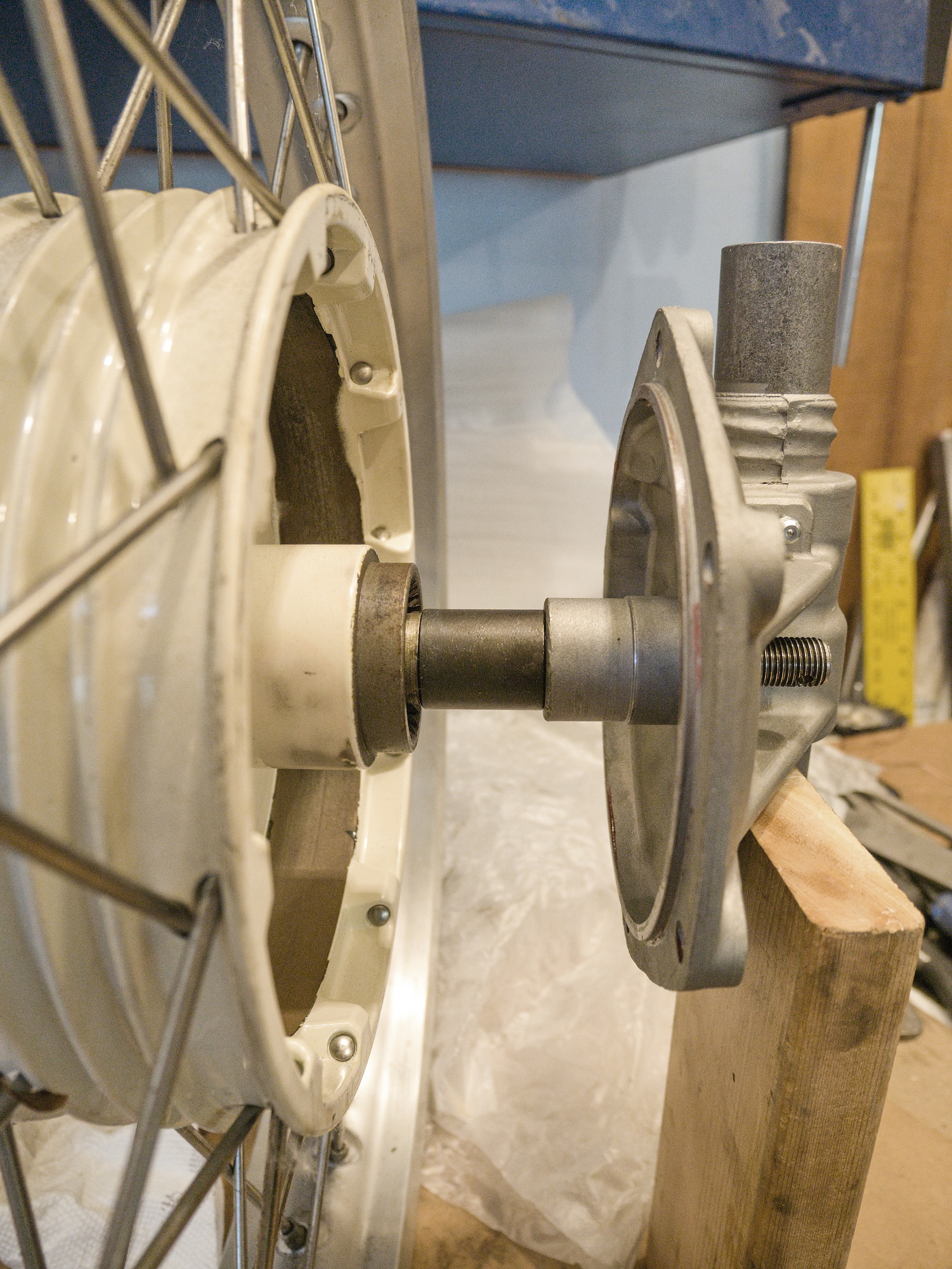

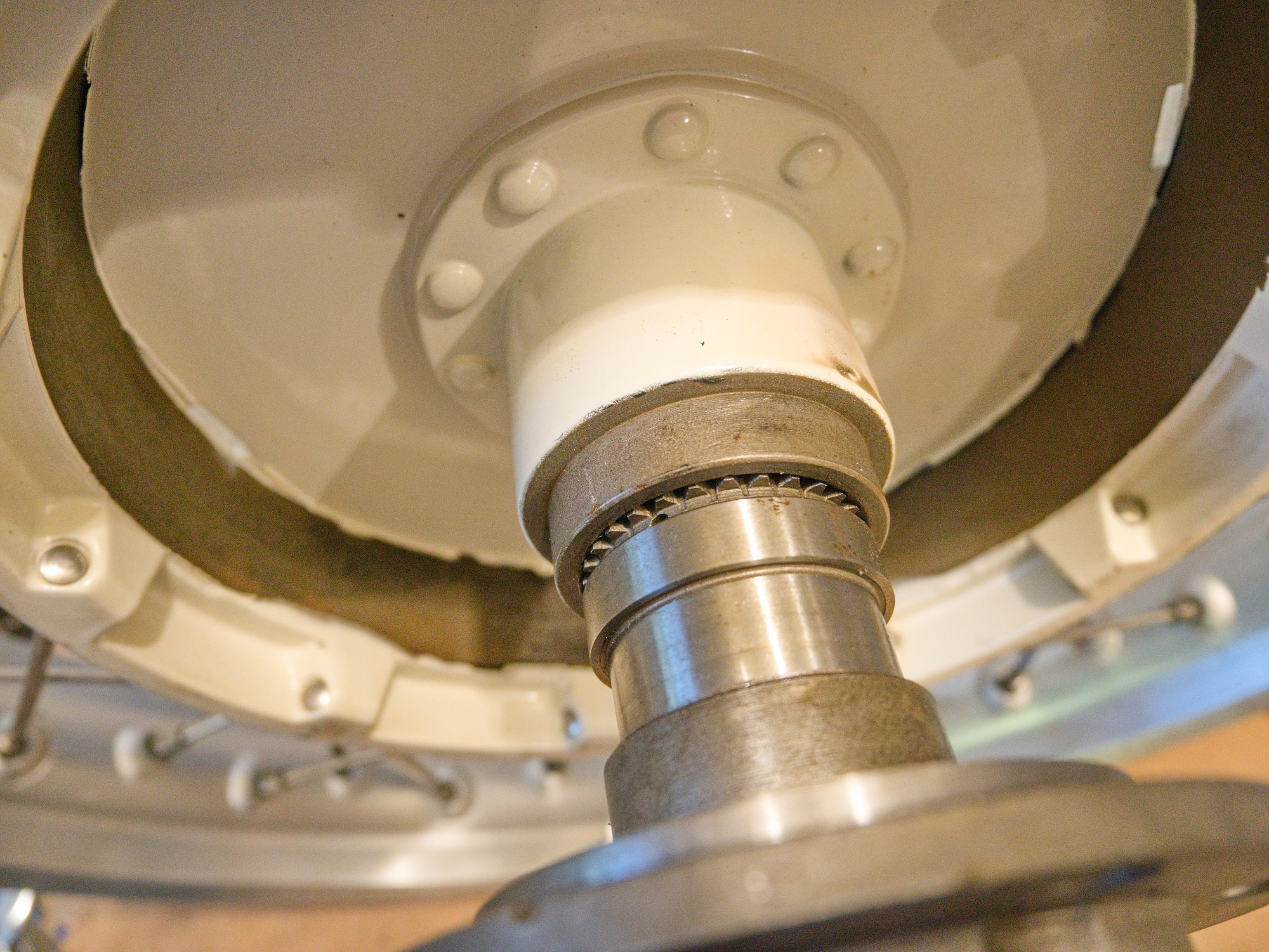
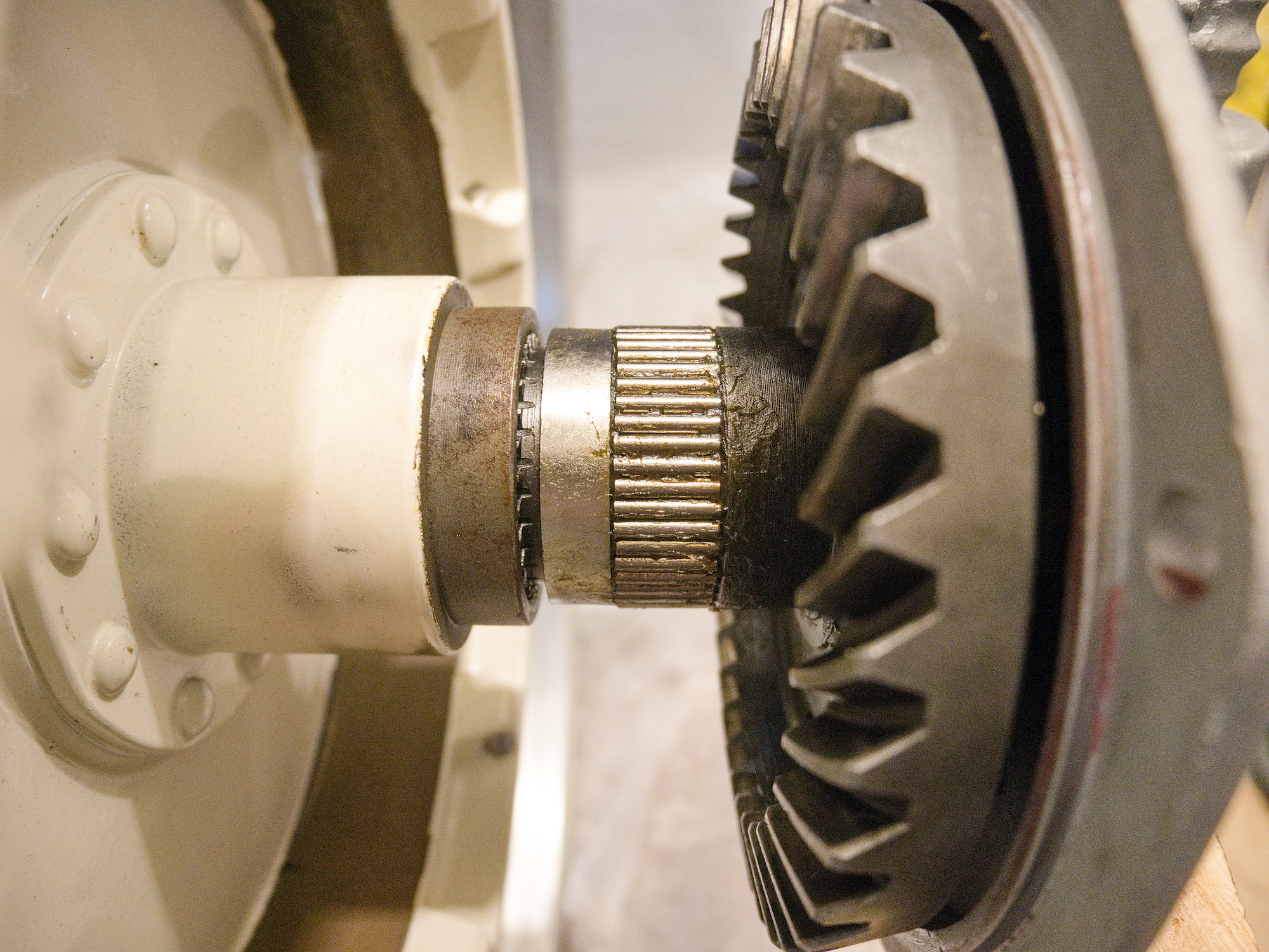

The M8x14 1.25 bolts, class 10.9, to connect the hub with the ring gear are secured with red loctite 272.
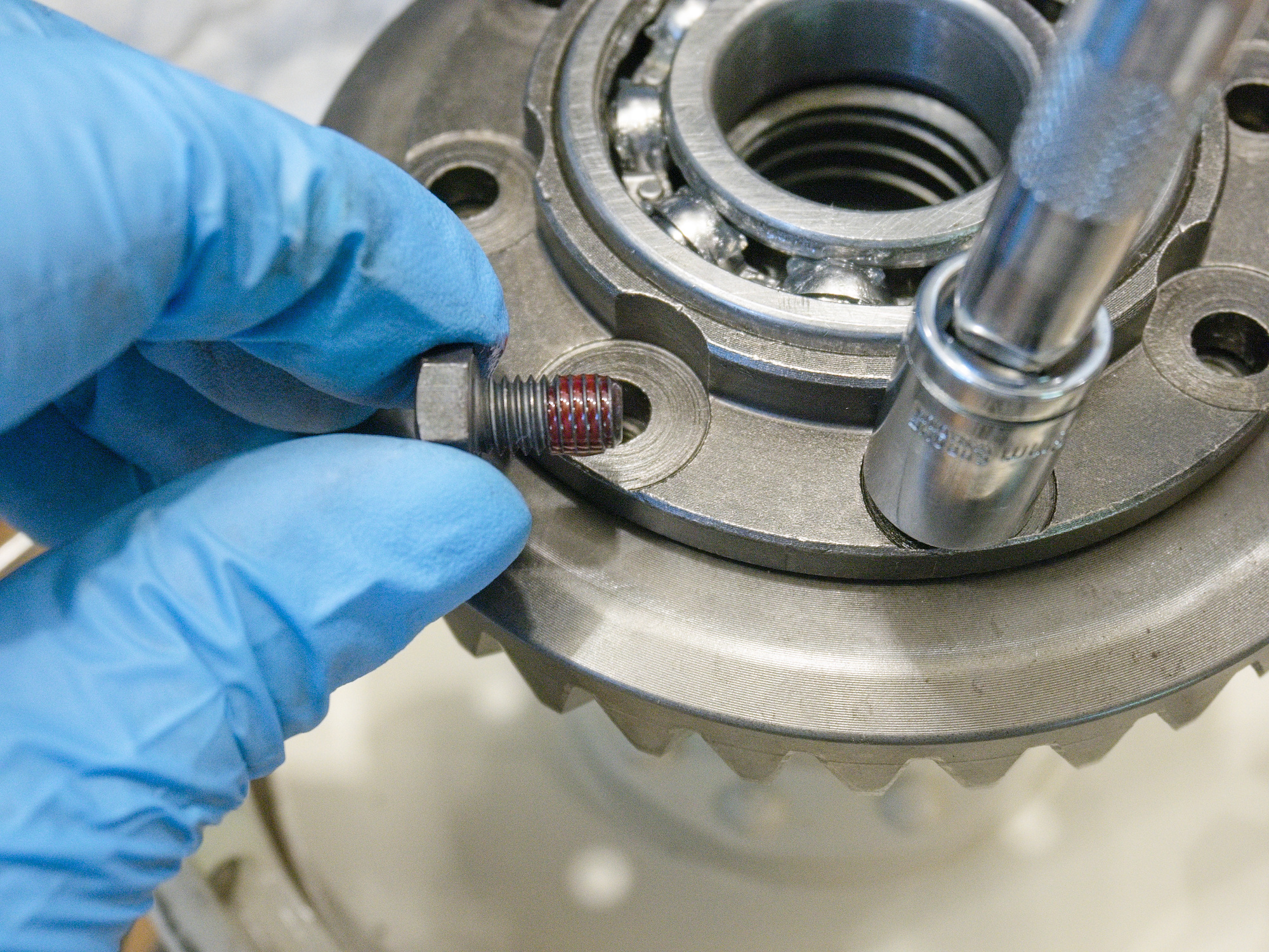
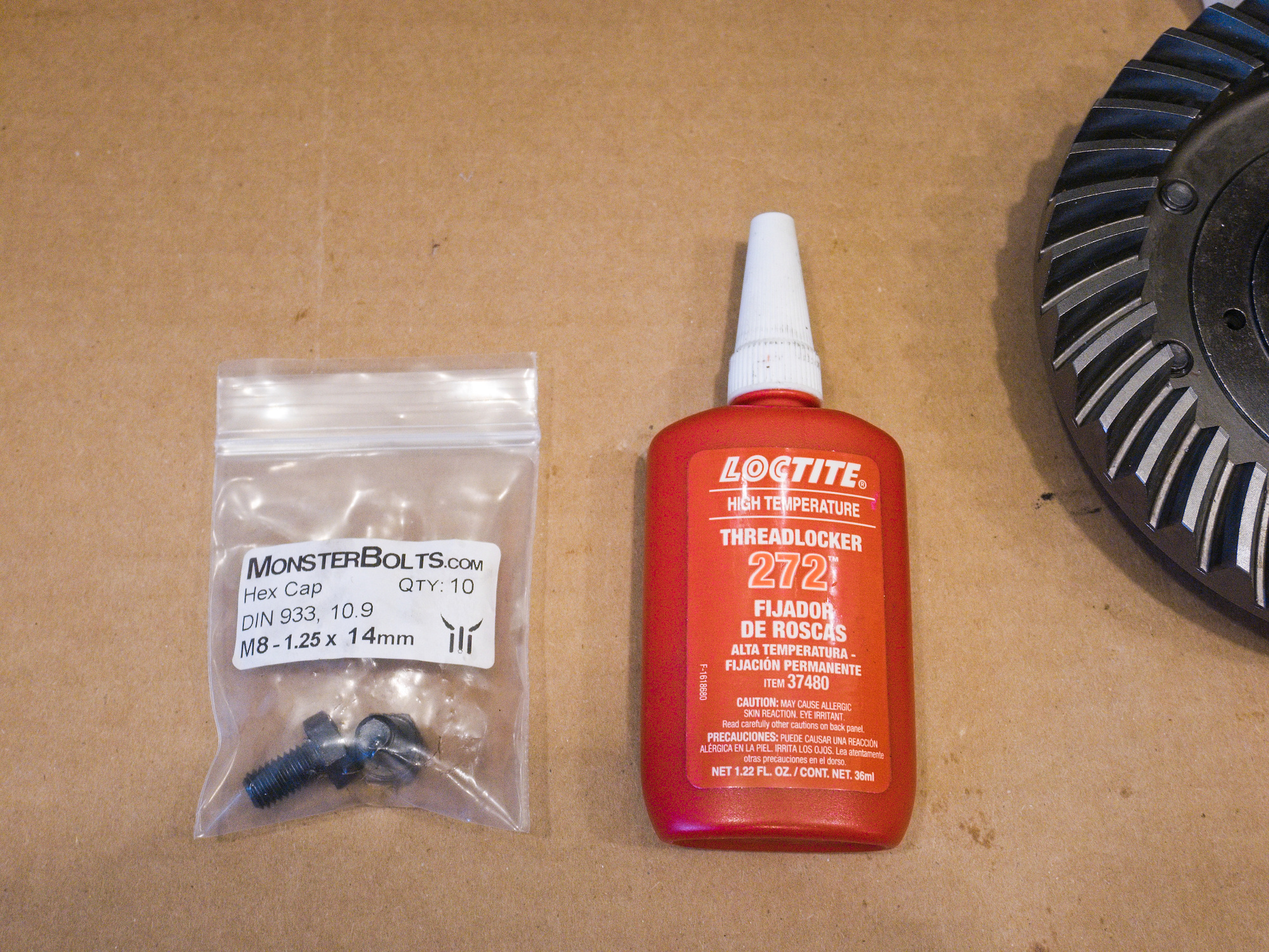
The bolts are torqued to 32Nm.
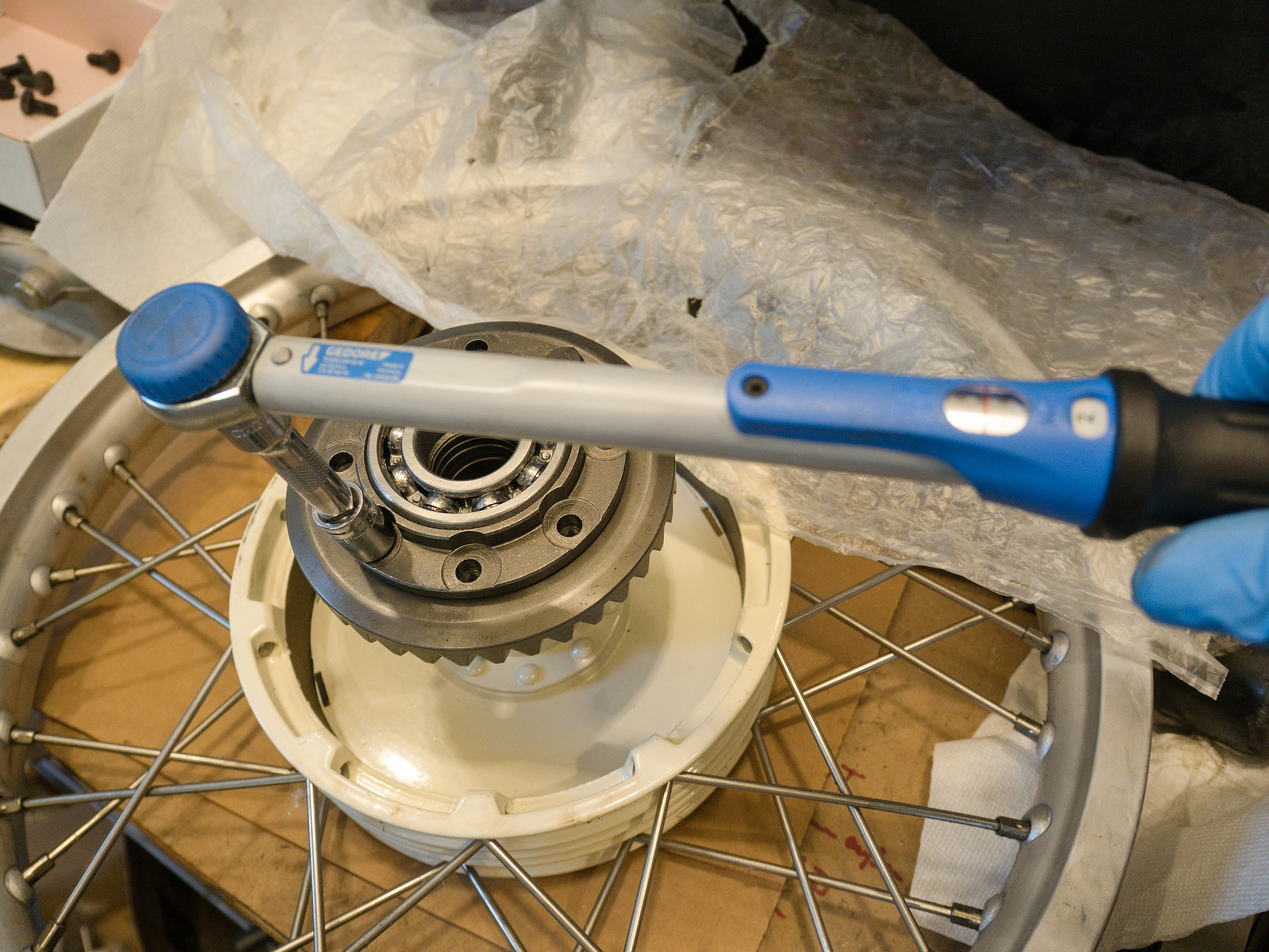
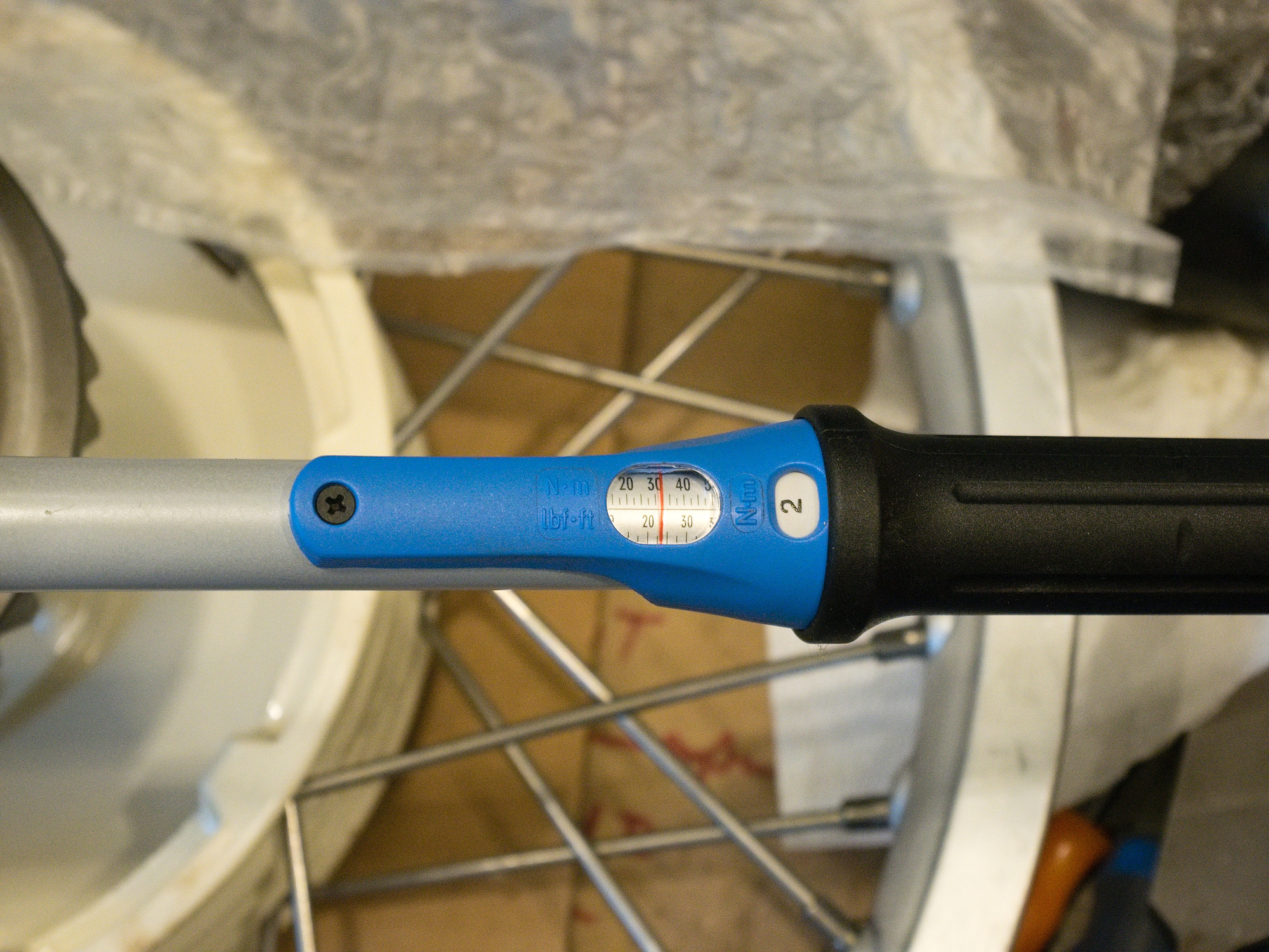
Clean the casing and cover surfaces and place the seal. Check the orientation as there is only one valid hole pattern. I used the one with EU quality from ural-zentrale.
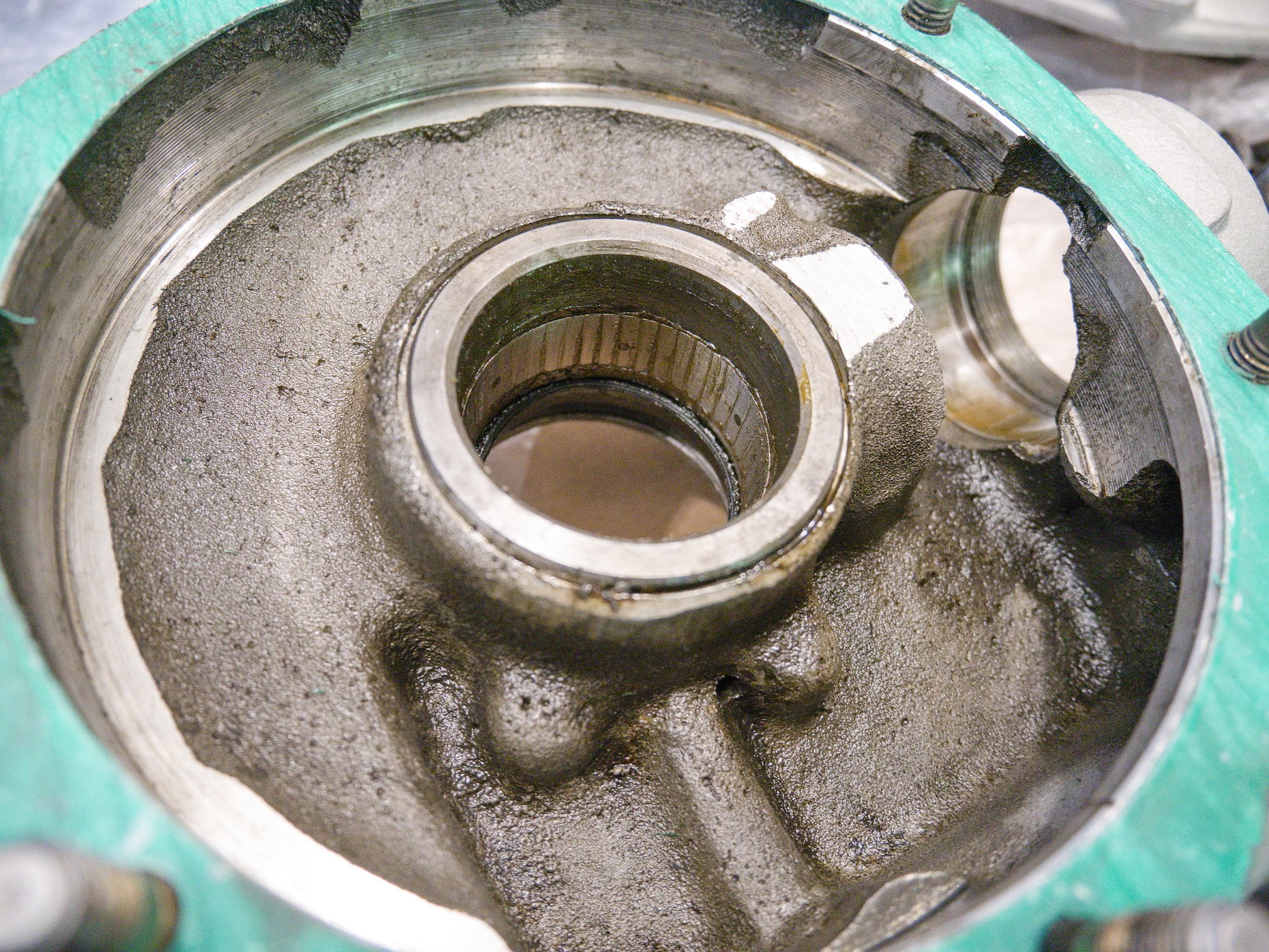


The suspension spring on the old final drive (FD) needs to be removed as it is reused for the new FD. It turned out that the measurement of the new suspension spring is different from the old one. It is only a small amount, but left and right suspension side need to match.
Level 1 of spring removal
The cap of the spring has a small hole to access the end of the spring and can be tapped out with a punch through the small hole. Simply twisting the spring will not work as the spring tightens when turned. Tapping will move the spring the opposite direction to unscrew from the holder.
Not the case here.
Level 2 of spring removal
Small access hole in the cap is not in the correct position and cap needs to be turned to access the end of the spring.
Not the case here.
Level 3 of spring removal
Everything is stuck. The cap won't turn, and the end of the spring is in a position that is not accessible to tap out.
This is the case here.
The surgery starts with the removal of the cap. The endmill is positioned to not cut all the way through the metal to not damage the spring.


Carefully bending back and forth.

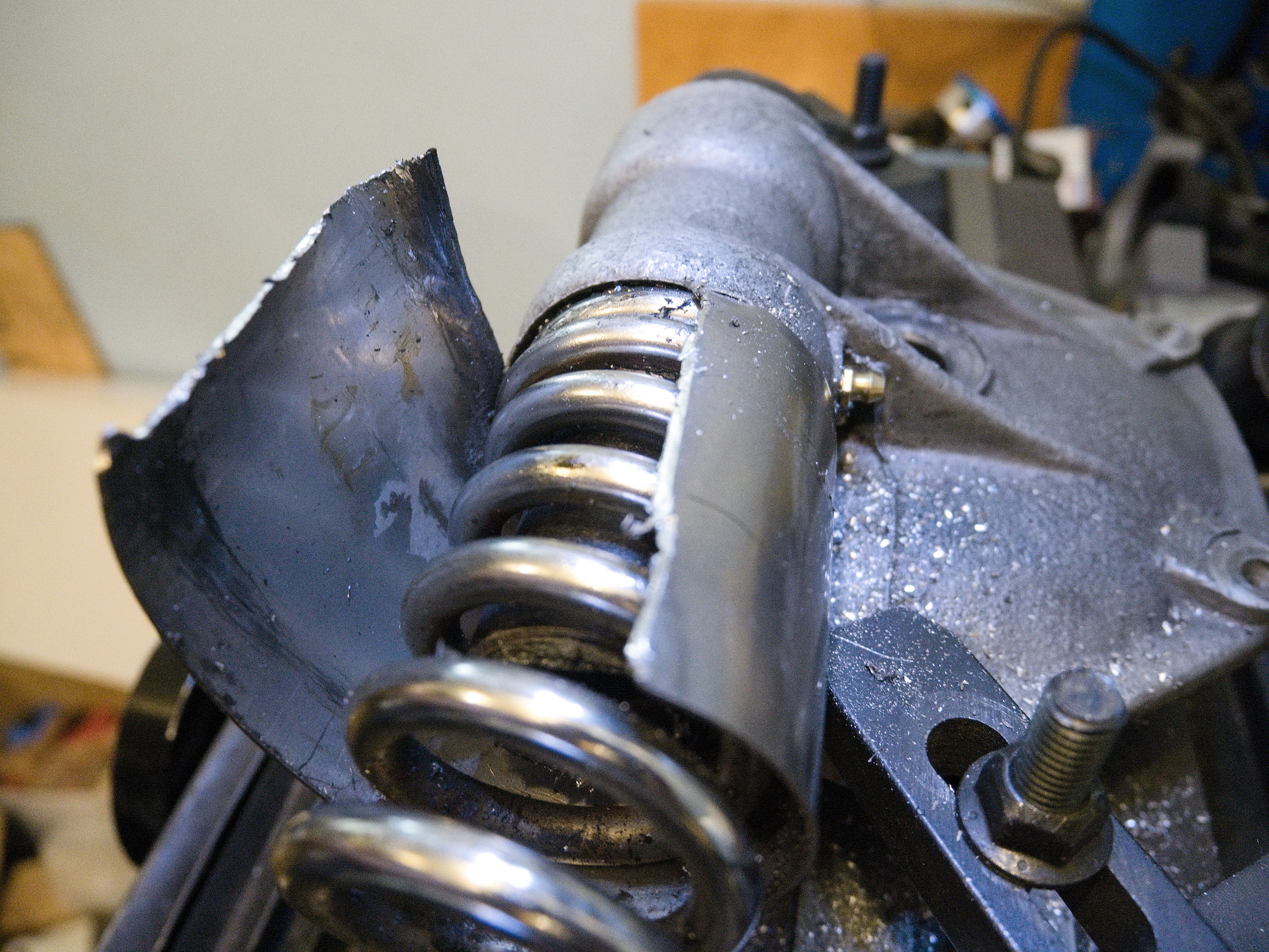

To try to turn the spring, a spanner is modified to hook into the end of the spring.

The position of the end of the spring is tight. The spanner need to be rather thin on the end to reach the spring position. Usually it doesn't take too much force to get the spring started, but unfortunately the spring is too tight and the spanner fails and the end of the modified spanner breaks.
Upgrade to level 4 of spring removal.
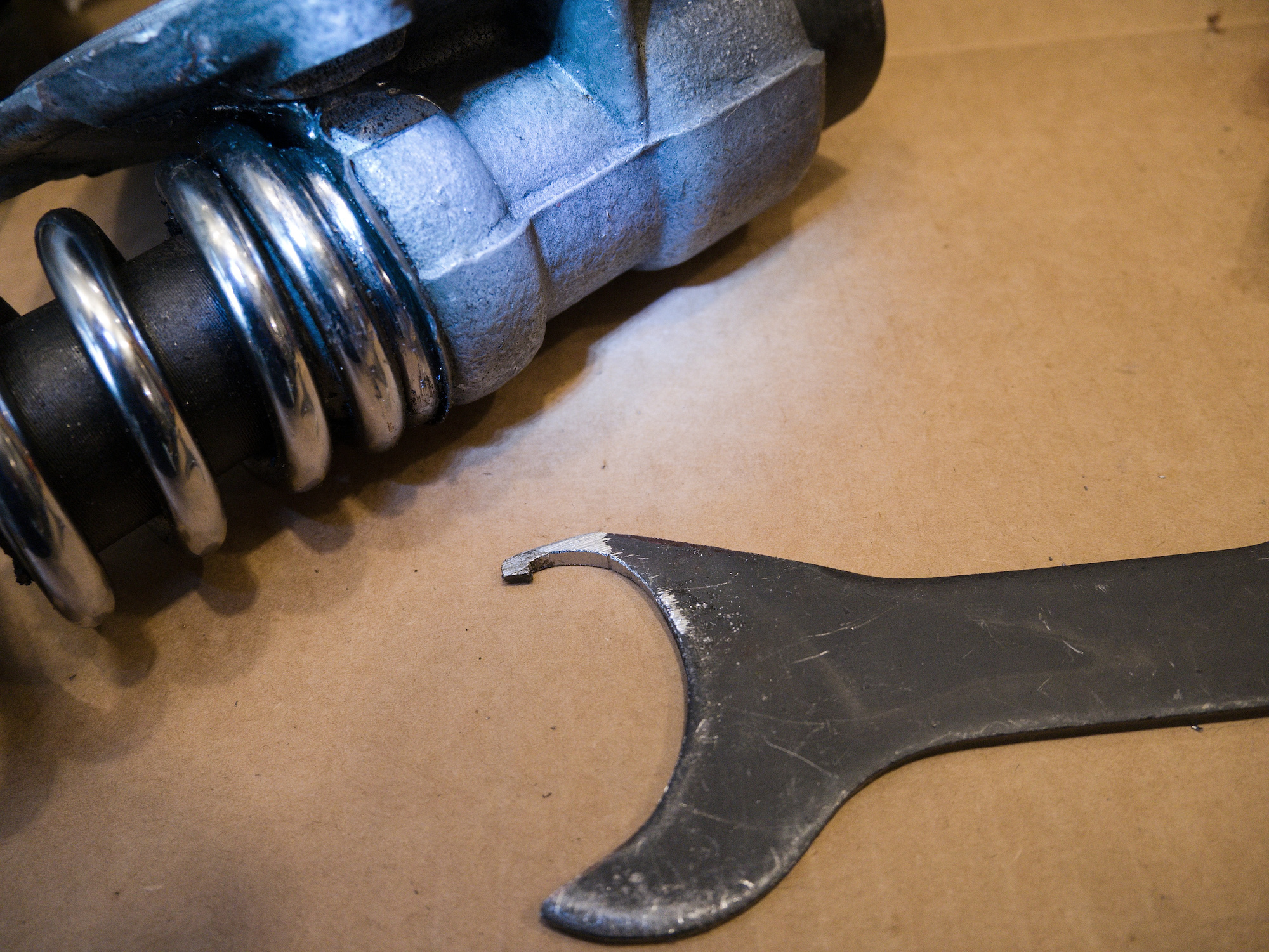
Level 4 of spring removal
The cut.
I have only this perfectly matching spring, but enough of FD covers. The cover needs to go.

The spring tension cause the blade to break and get stuck halfway through the cut.
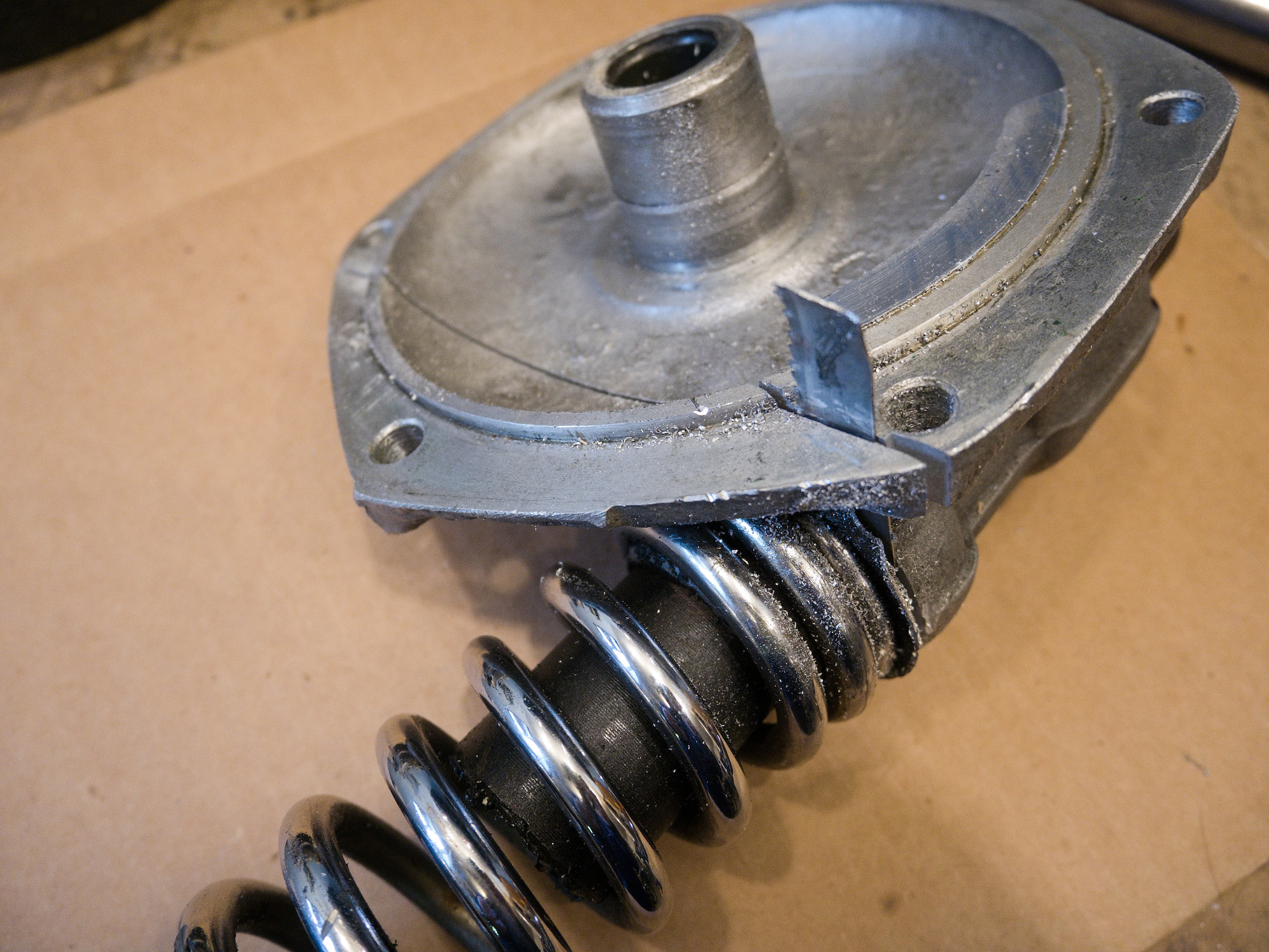
The spring is separated, but the guide for the suspension rod is still stuck.
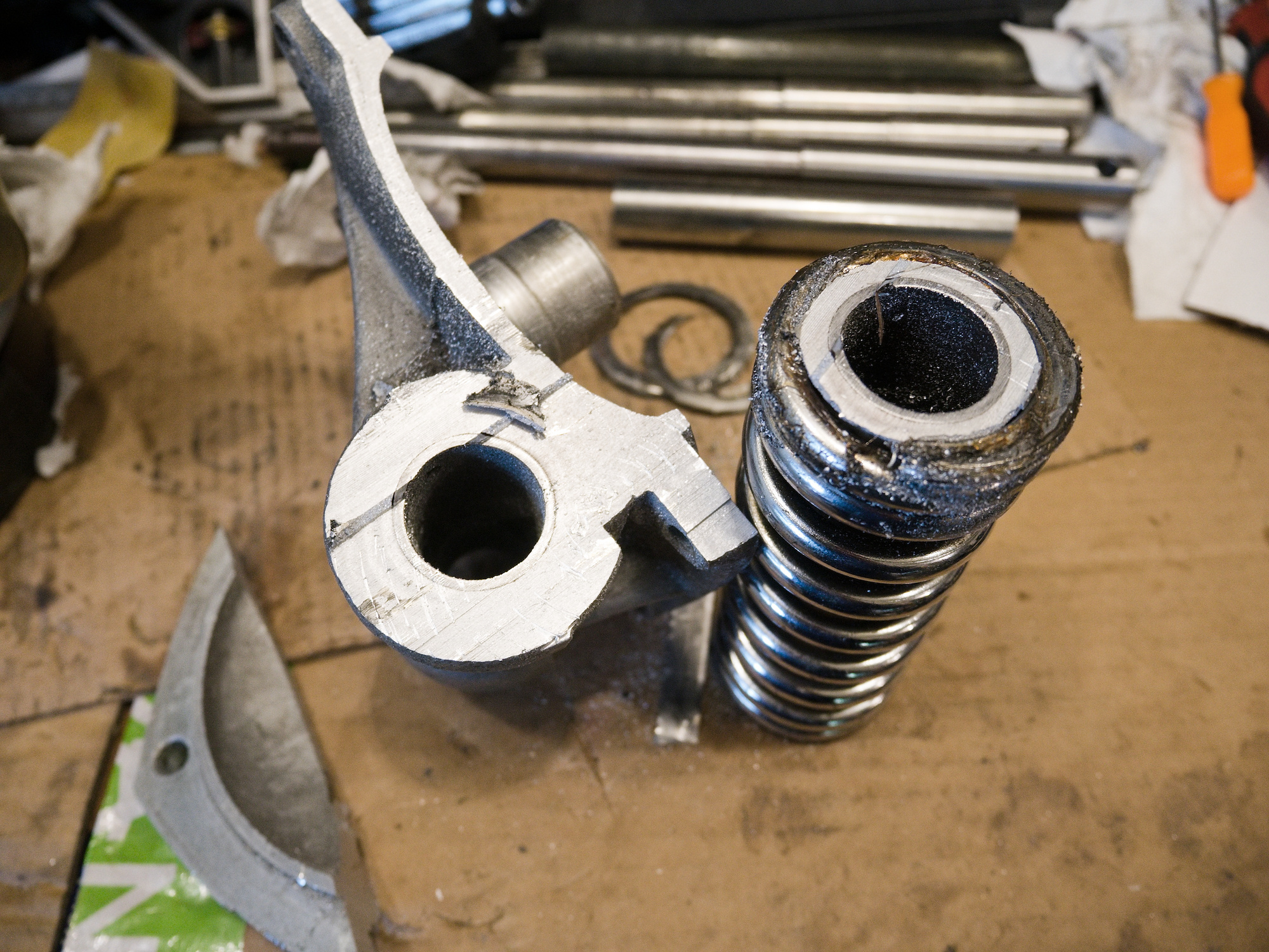
The plan is to make a saw cut from the inside.
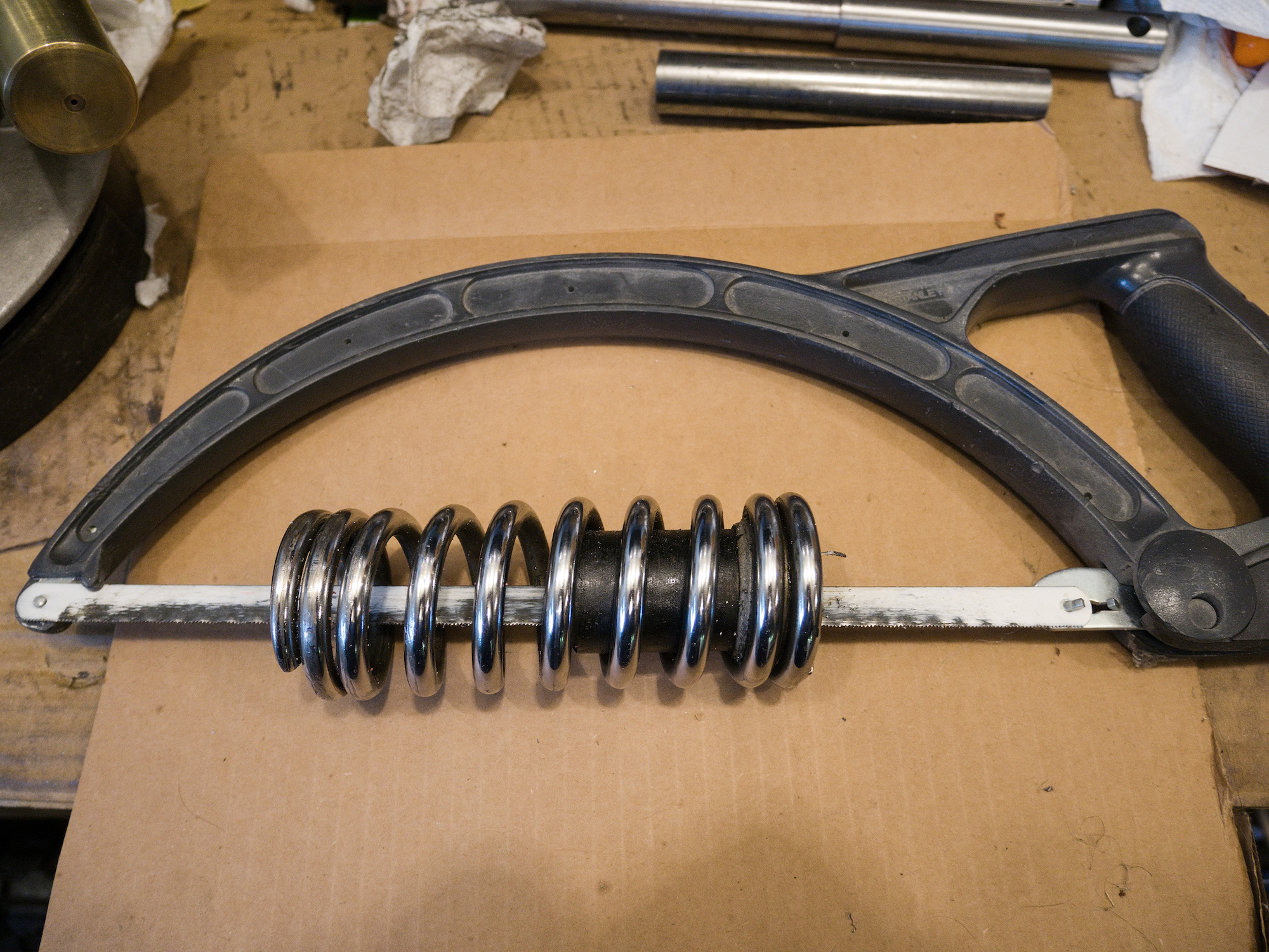
The guide consists of two parts. The inner part can now be tapped out.
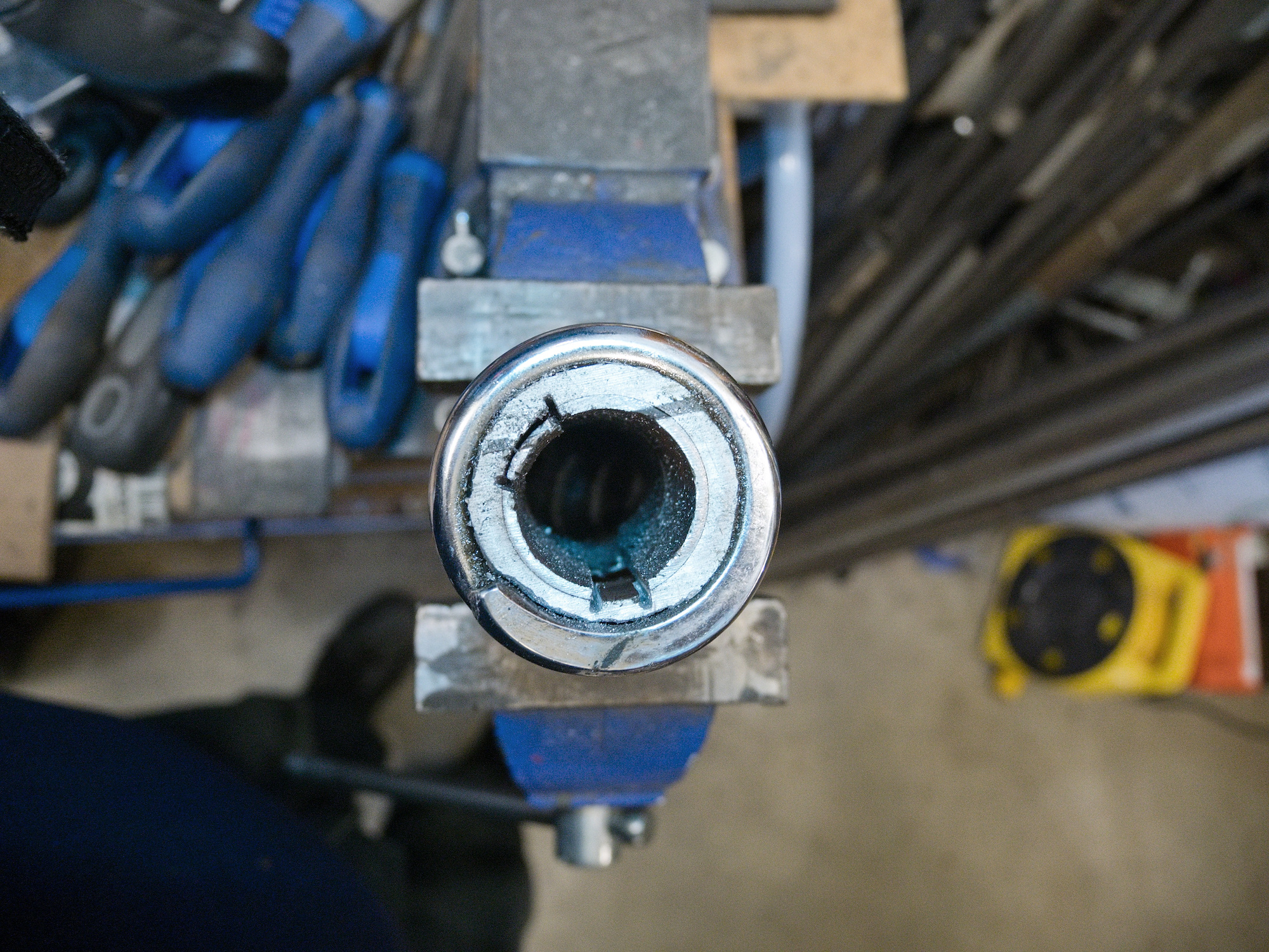

The outer part of the guide needs to be very carefully cut to not damage the spring.
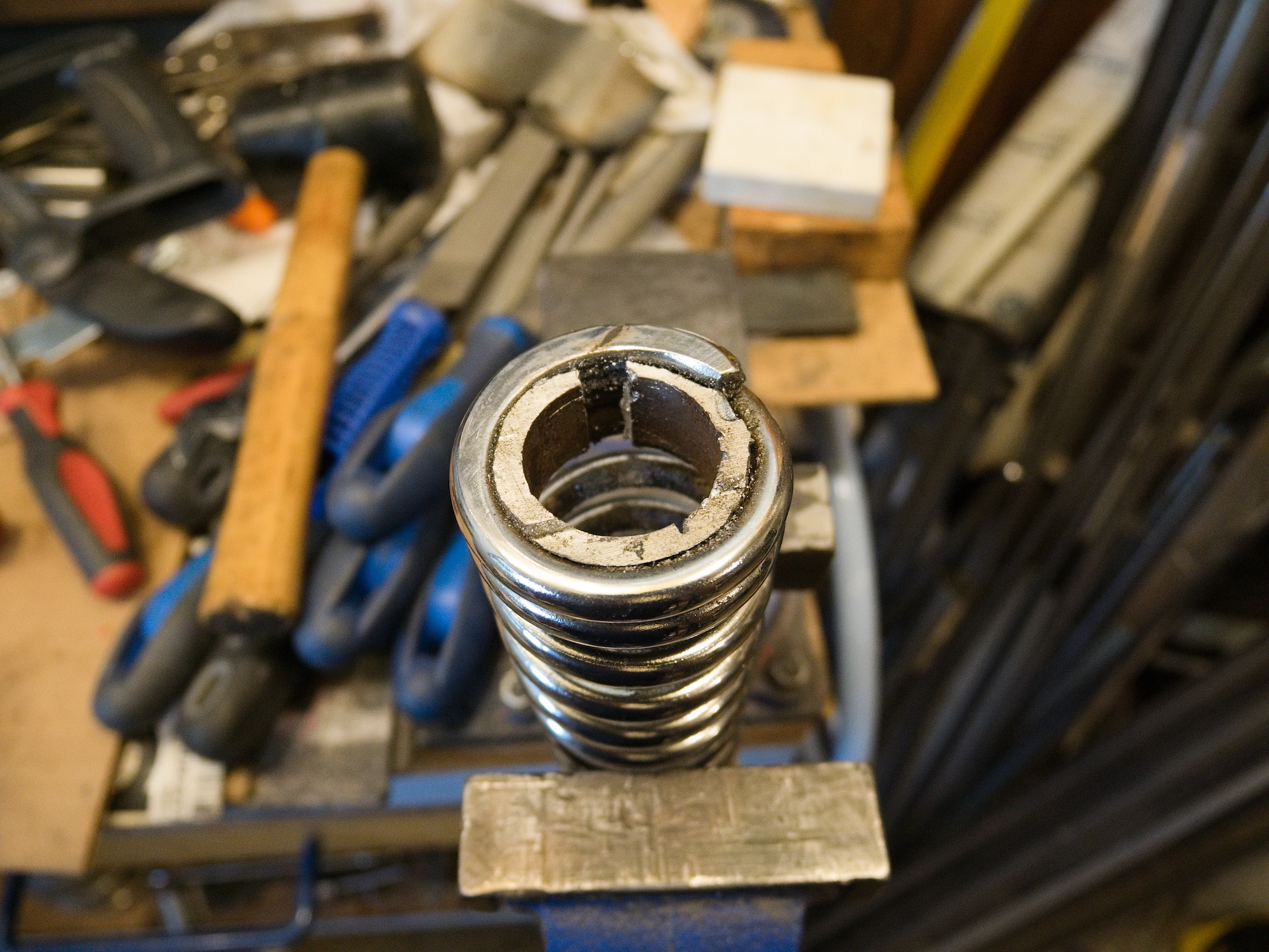
Left side is the newly ordered spring, right side is the rescued spring.
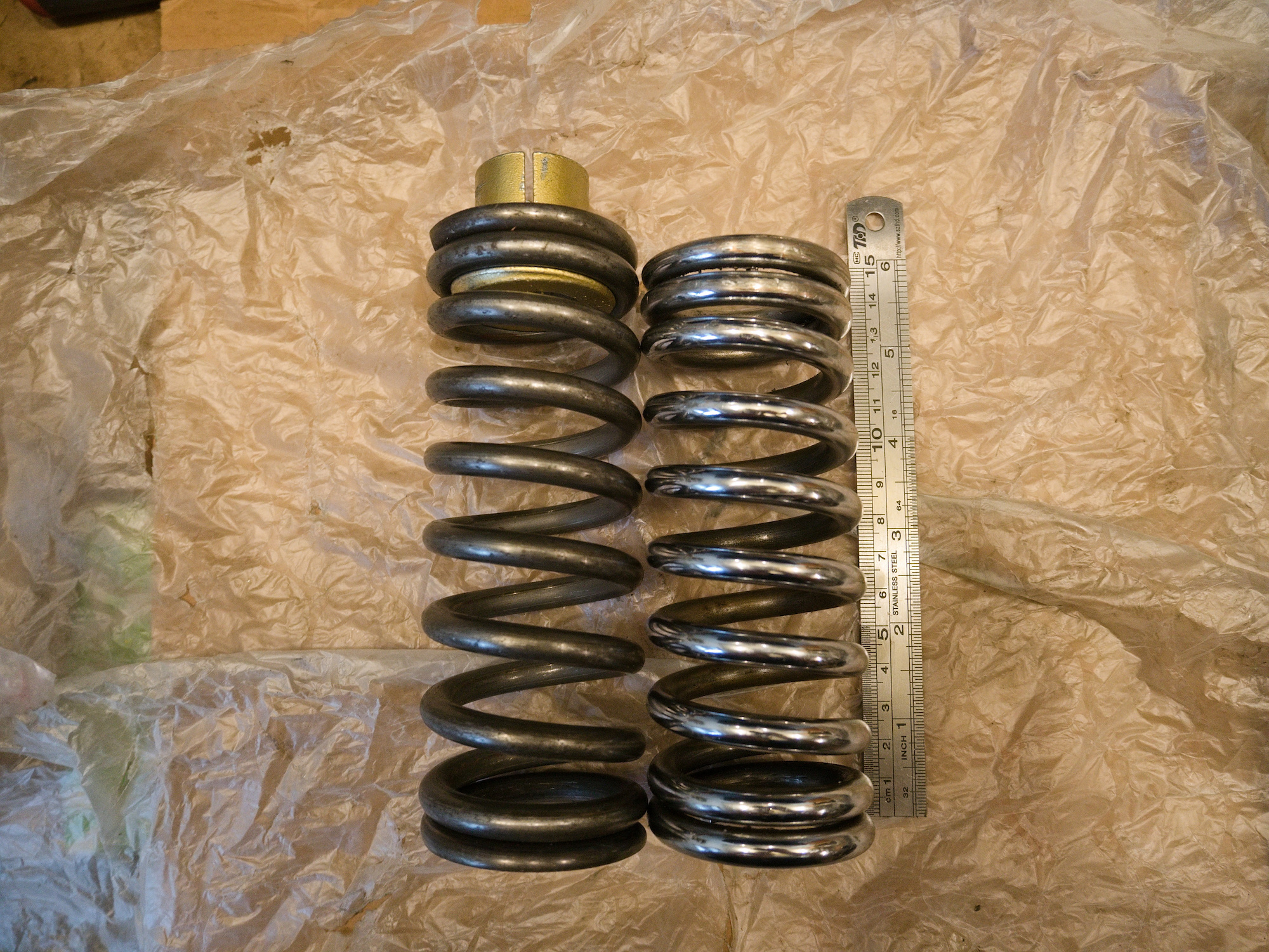
Not only have the CJ750 and M72 the same final drive (the thingy that connects the back wheel to the gearbox), but they also share the same Ring and Pinion gear of the Ural Motorcycle.
With the Ural 2019 and newer, final drives now running an European Ring and Pinion gear. Here I show you how to use those to upgrade your final drive (FD). So no more Russian or Chinese Junk!
See the Interview with Ural on youTube starting from 0:23 with details on the new gear set.
The European Ring and Pinion set is IMZ-8.128-05048 and has a 37/8 ratio.

Left side is my old one. Right side is the new one from the Italian production. Italians are specialized in flat round things (Pizza).
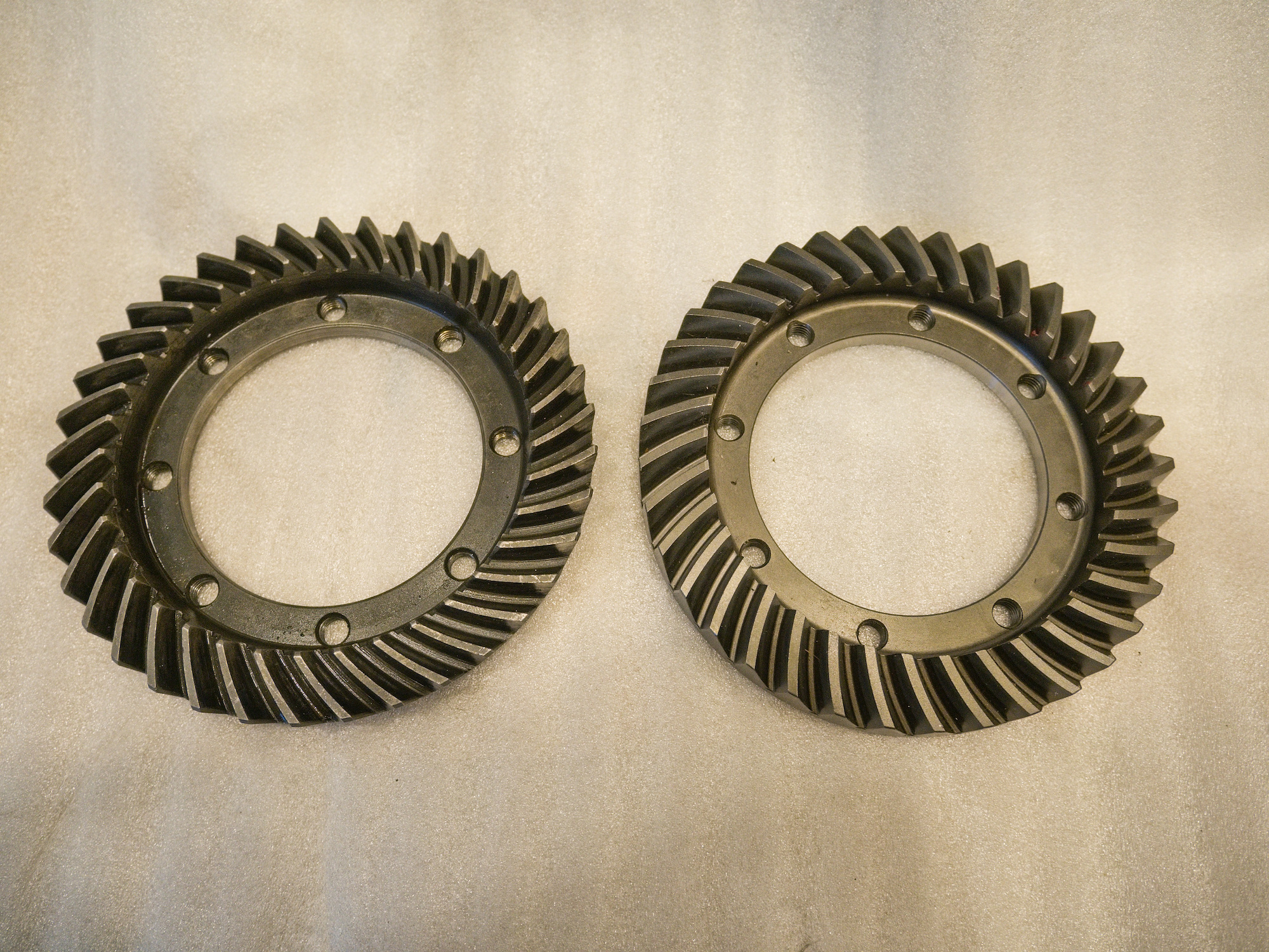
Bottom is the new one.
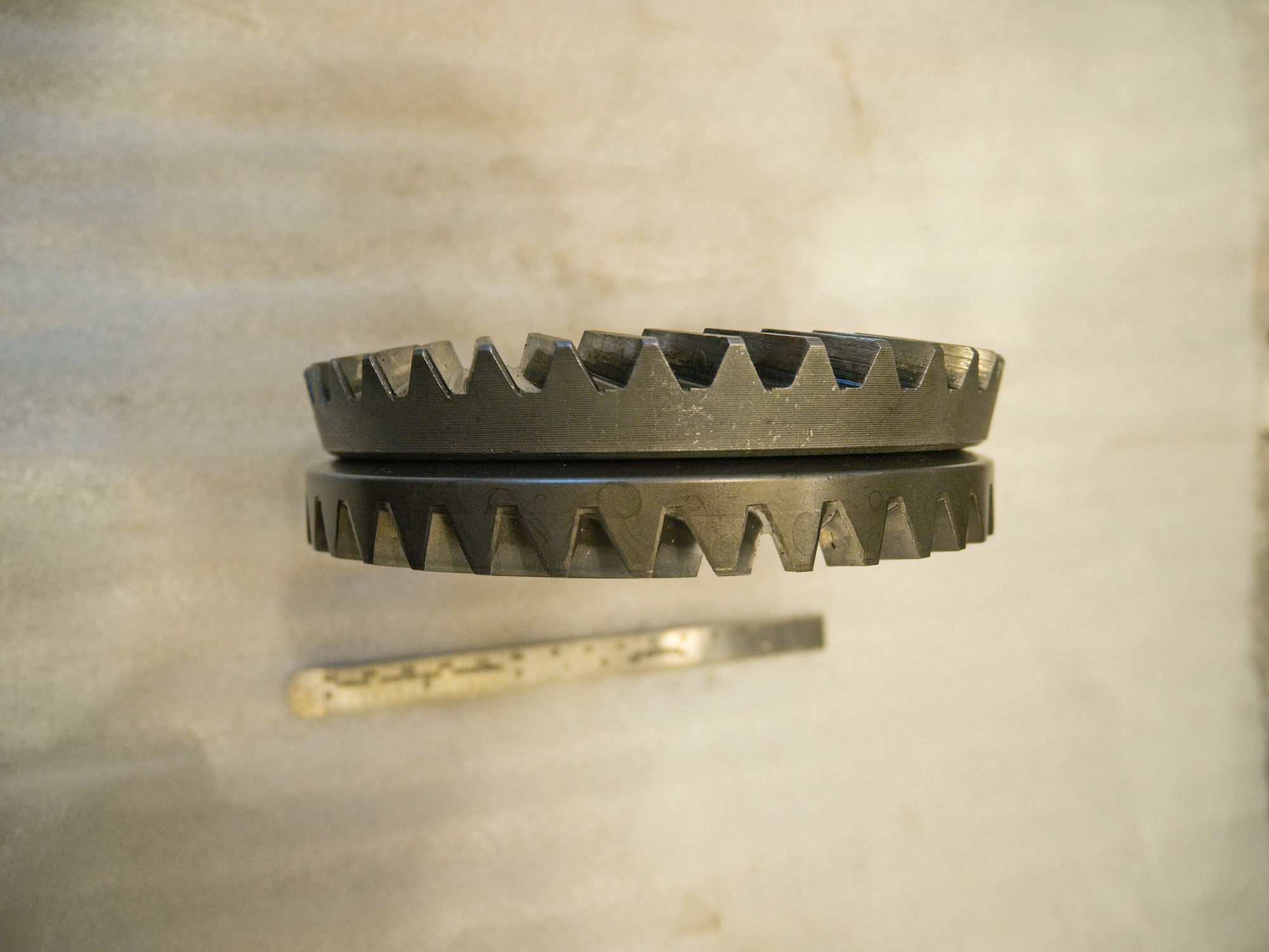
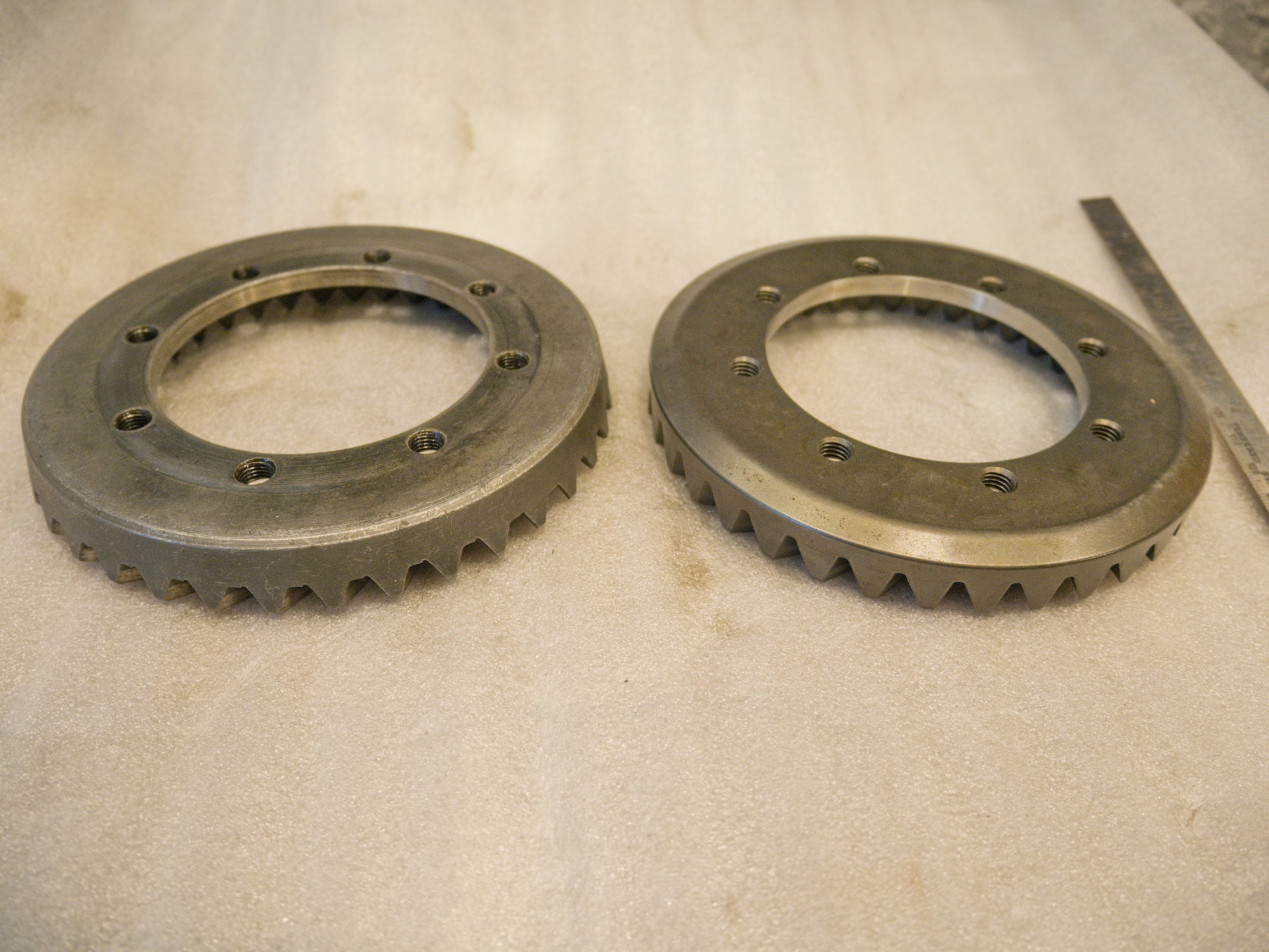

Bearings:
Ring bearing 6207c3
(35mm bore, 72mm OD, 17mm width)
Pinion bearing 3304
Bearings can have different properties. For example:
3304 A-2Z/C3
Angular contact ball bearings, double row
- 2Z: Shield on both sides (Z is for metal shield)
- C3: Internal clearance greater than Normal
3304 A-2RS1
Angular contact ball bearings, double row
- 2RS1: Contact seal, NBR, on both sides (RS is for rubber seal)
C2: Clearance less than normal clearance
C1: Clearance less than C2 clearance
C3: Clearance more than normal clearance
C4: Clearance more than C3 clearance
C5: Clearance more than C4 clearance
3304 A-TN9
TN9: Glass fibre reinforced PA66 cage, rolling element centered
The 3304 gets pressed on later to the pinion gear shaft. For the contact pattern, a plastic guide with the same dimensions as the bearing is used to make it easier to move the gear in and out of the casing.
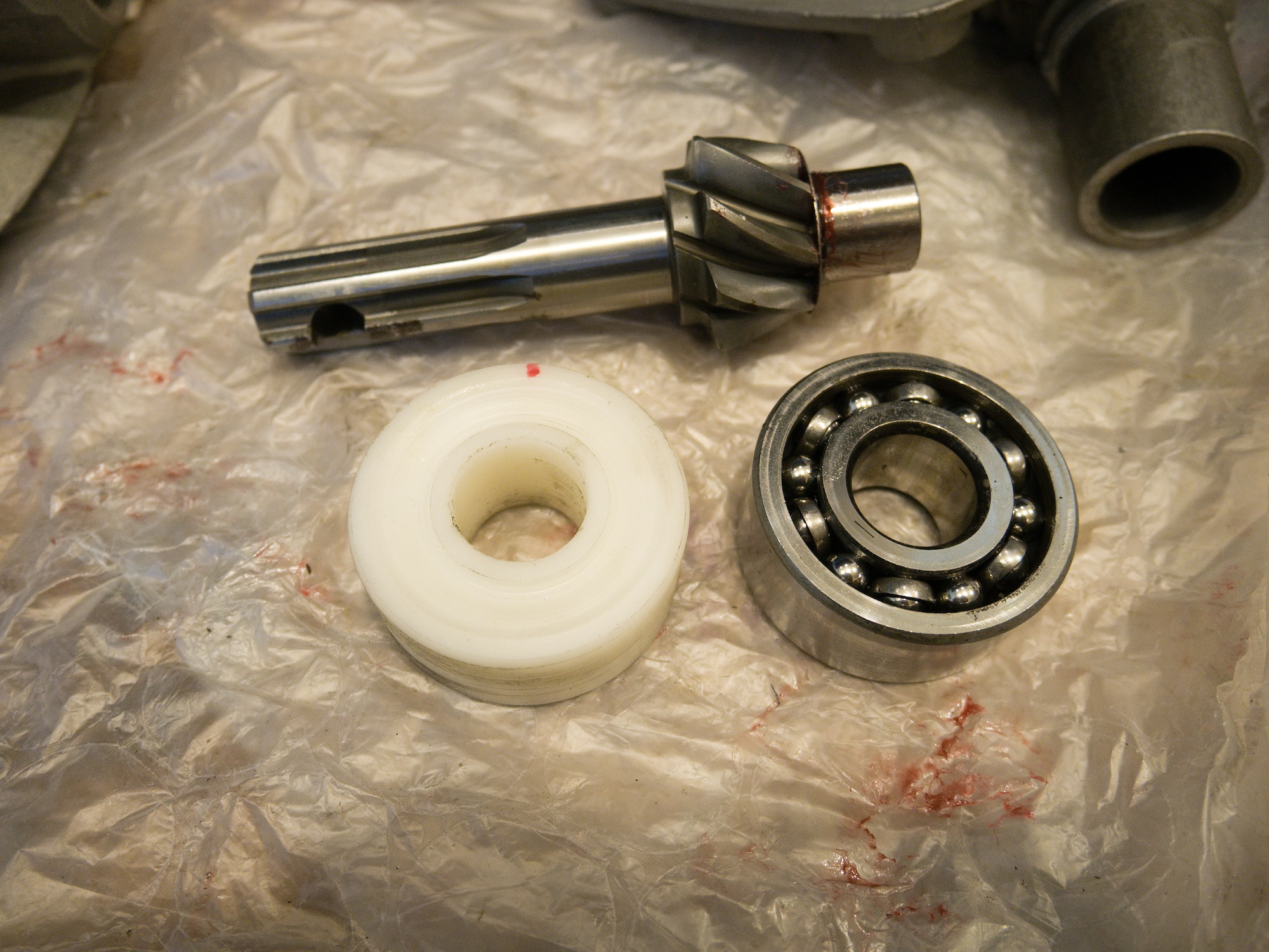
The following places are a good source if you want to start with new parts. I have used them all and they provided exceptional service.
- ural-zentrale
- oldtimergarage
- sidecarpro
- mhmotoworld ebay or mhmotoworld
Please be aware that shipping damage can happen despite the best efforts of the packaging. Like this bend, which is a quick fix. Project on!
Note: The M72 has only one stabilization fin on the housing, while the CJ750 has two as seen in this picture to make the housing more stable. But in general parts are exchangeable.
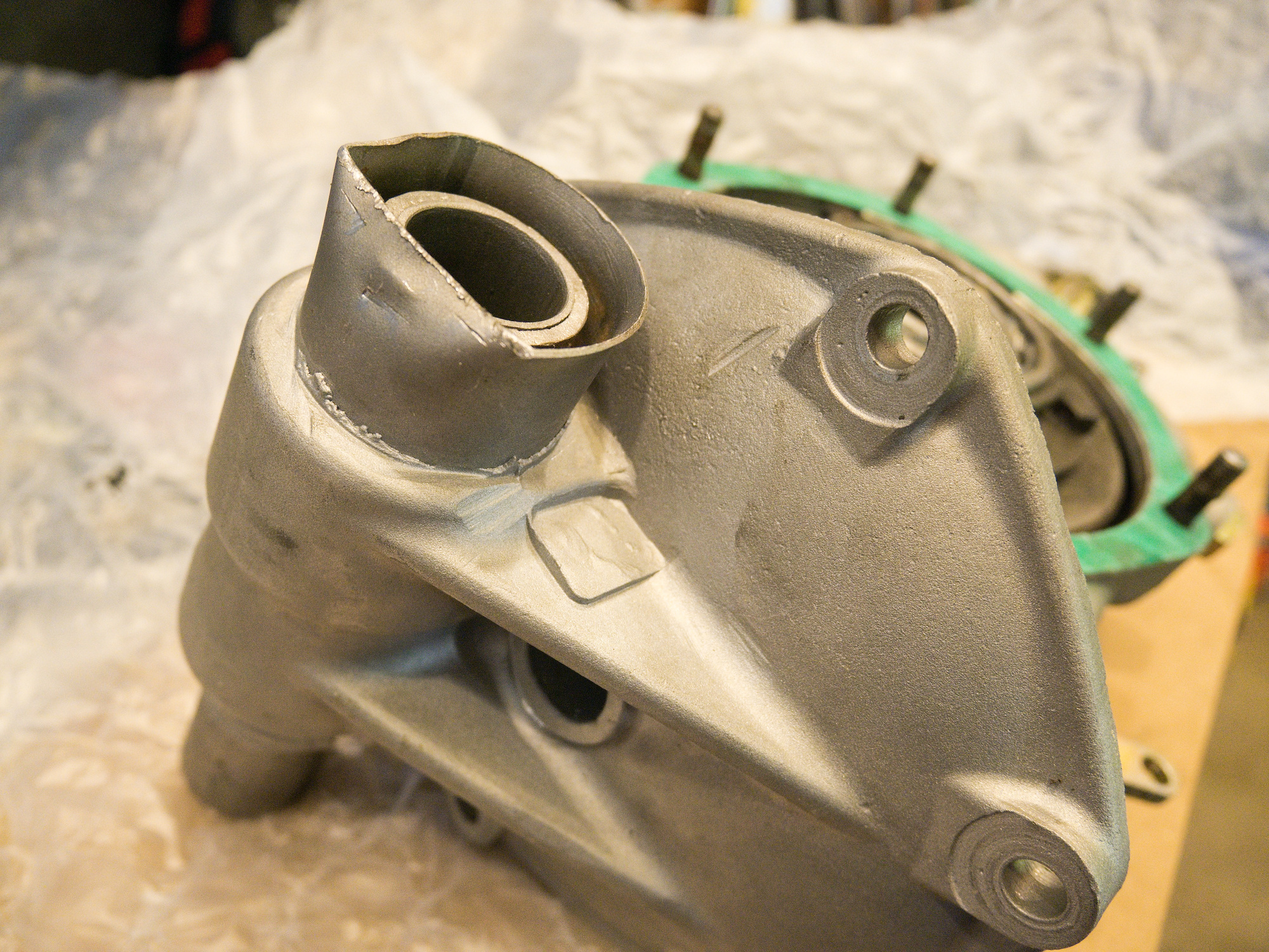
Inspect all parts, and make sure all oil channels are clear.
The oil drain from the main seal to the bottom is most important. It prevents oil contaminating the break shoes.
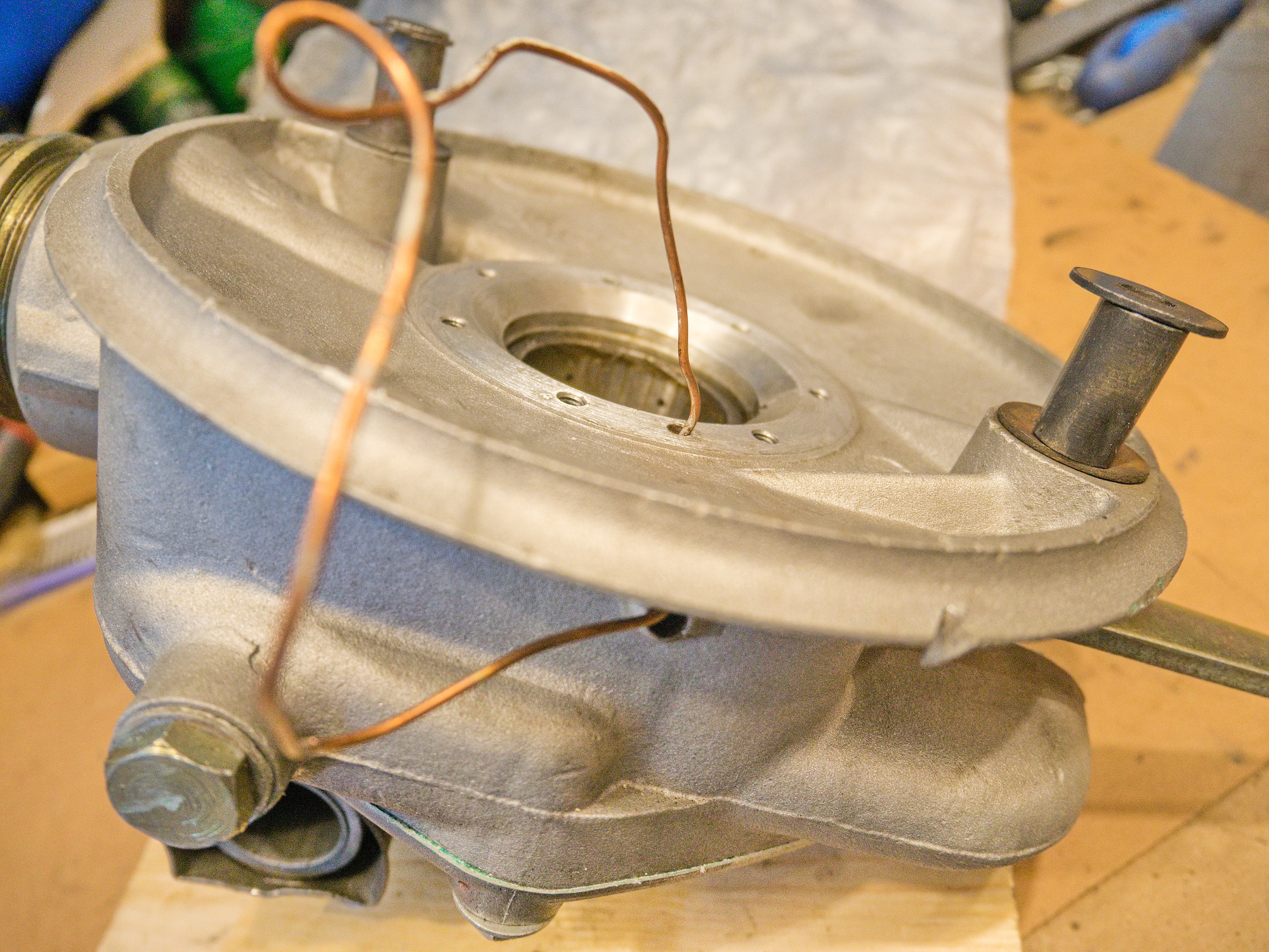
FDs consumables. My collection.

Pinion inner bearing
The pinion inner bearing is normally 20x32x20, but with the new pinion it needs to be 20x32x16. This is a NKI20/16 Needle Roller Bearing.
The existing pinion gear race in the FD needs to be removed. A simple task using a Blind Hole Puller (from a Blind Hole Collet Bearing Race and Seal Puller Extractor Kit in case you are looking for such puller), and a piece of protecting plastic.
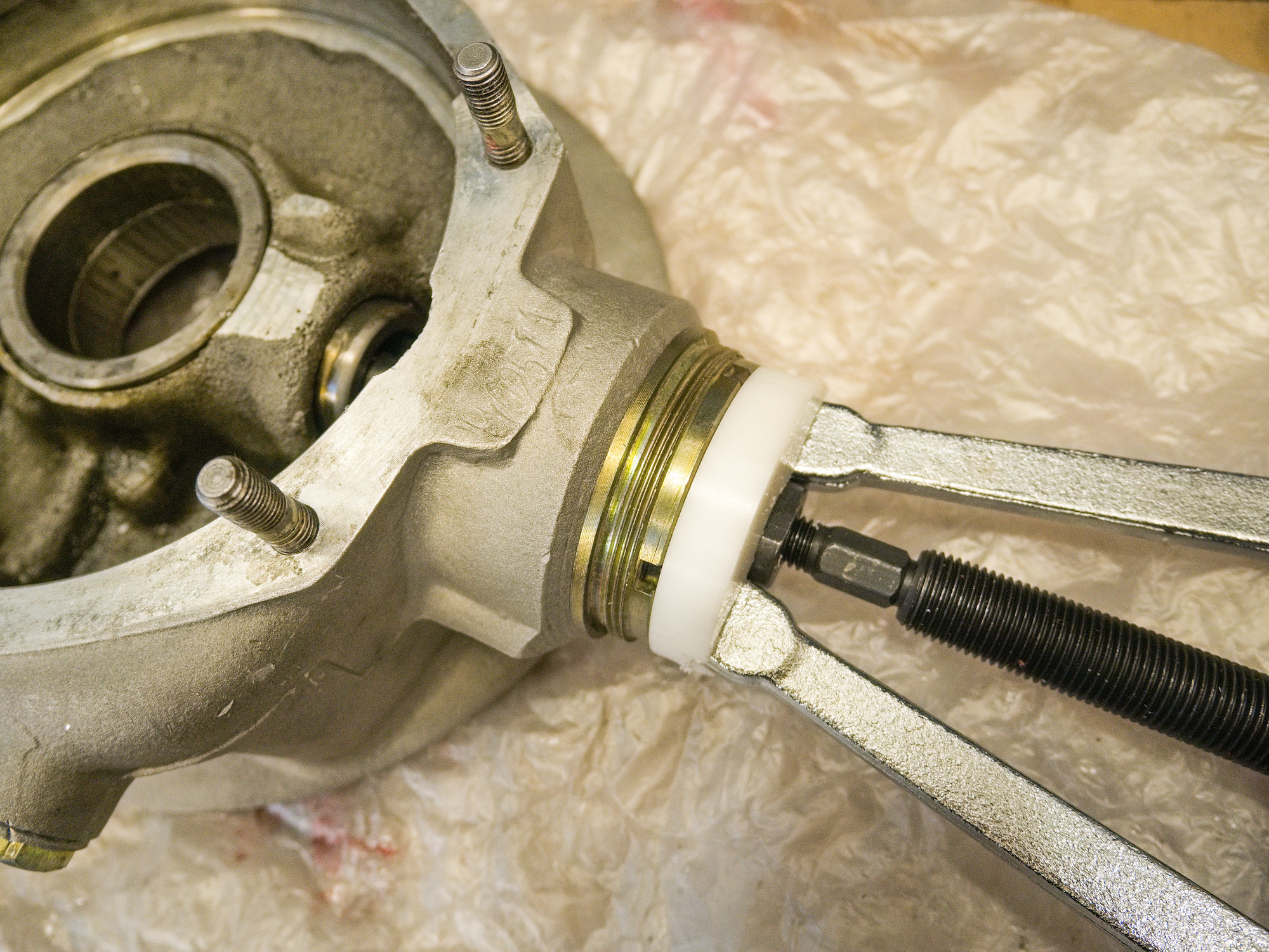
Make sure the tiny hole to the main bearing is also clear.
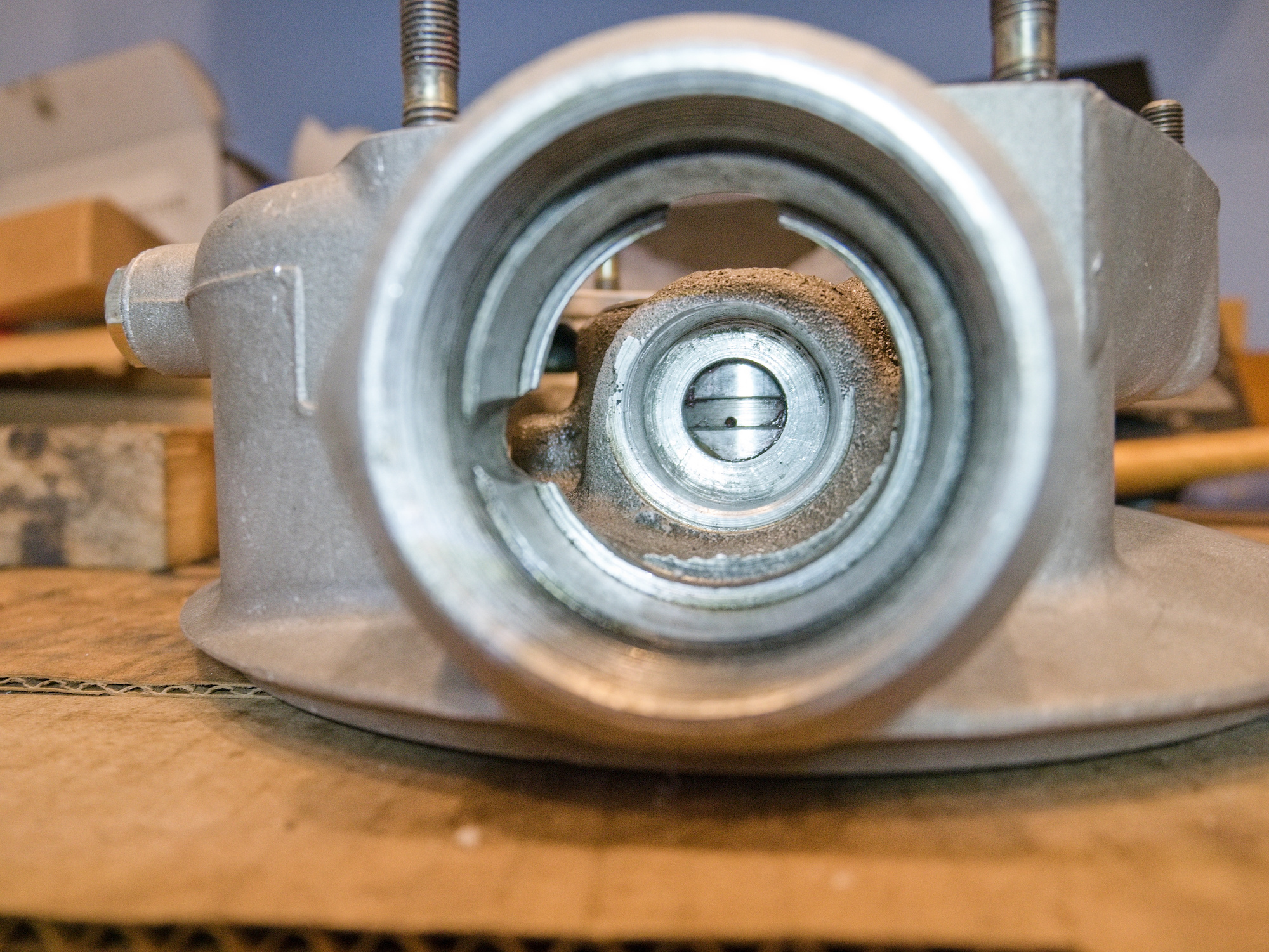
Benzinkanisterhalter, Teil 3, das Montieren
Der Halter für die Halterung wird an der Innenseite des Beiwagens montiert. Der Vorteil dieser Halterung gegenüber einfachen Schrauben im Blech ist in der Kraftverteilung. Das Blech verformt sich bei großer Last nicht:

Der Bügel wird mit einer Feder gespannt und hält den Benzinkanister.
Das Auslaufrohr wird auf die schwarze Halterung gesteckt.
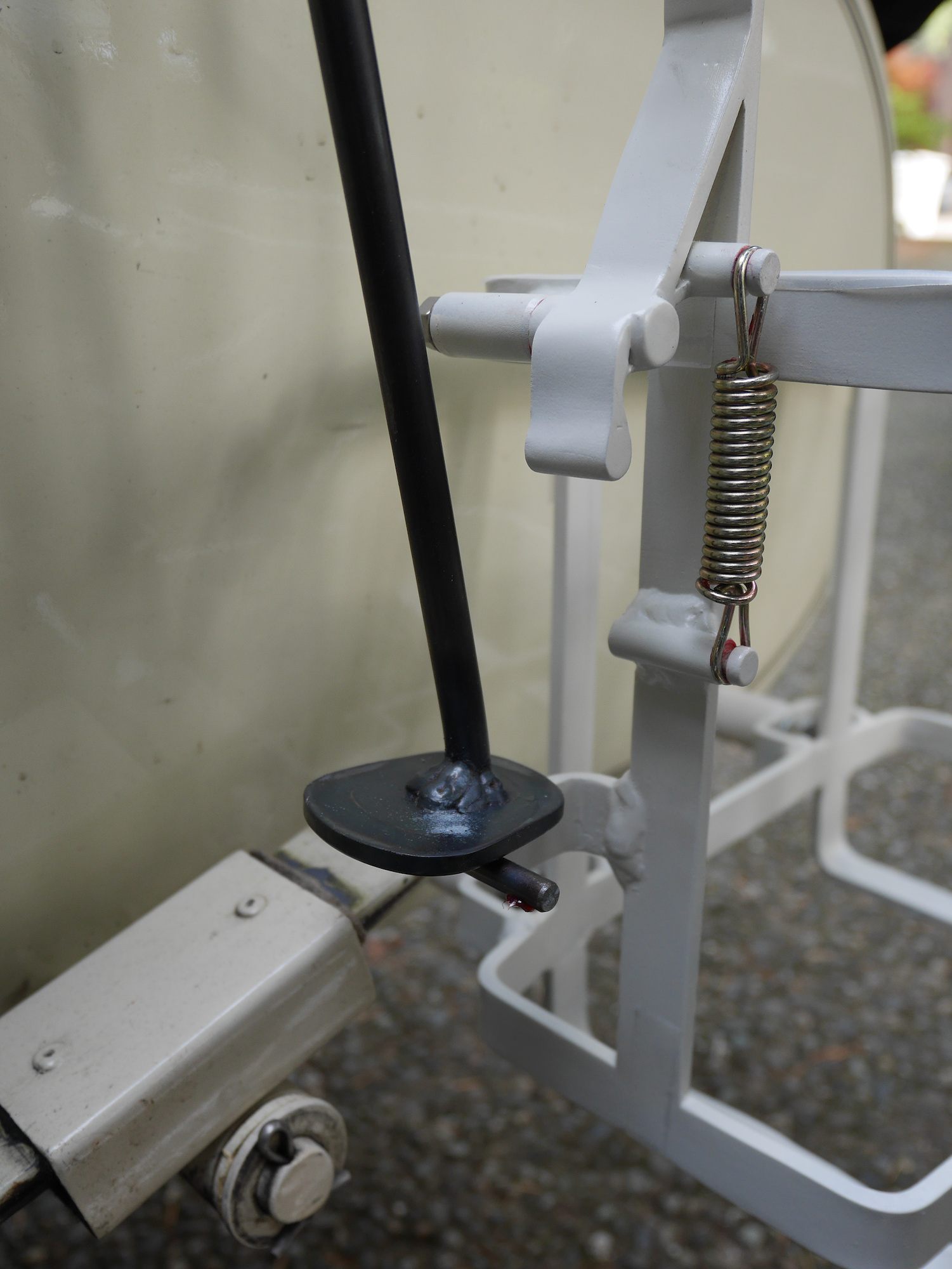
Fertig montierter Benzinkanisterhalter:
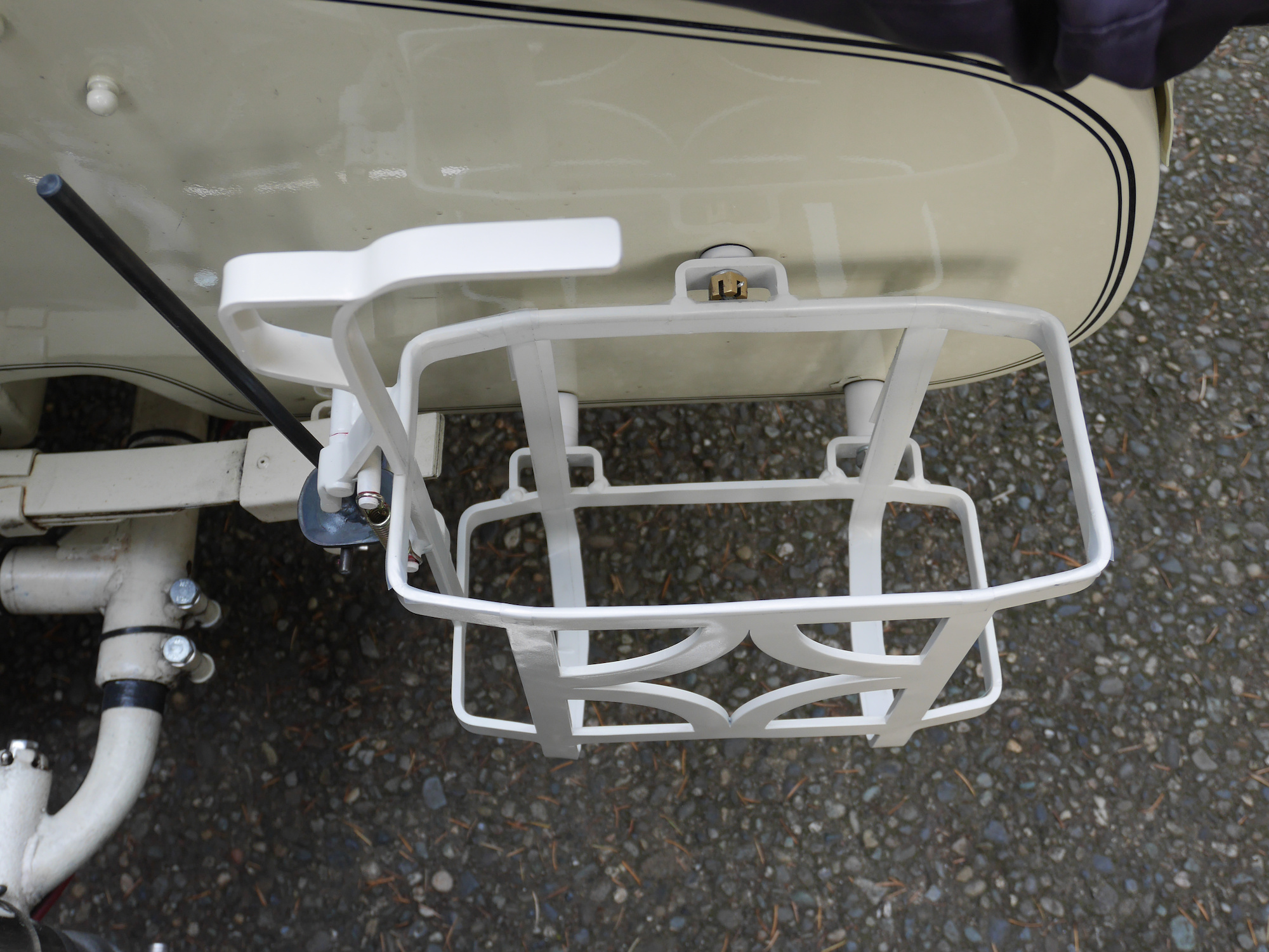
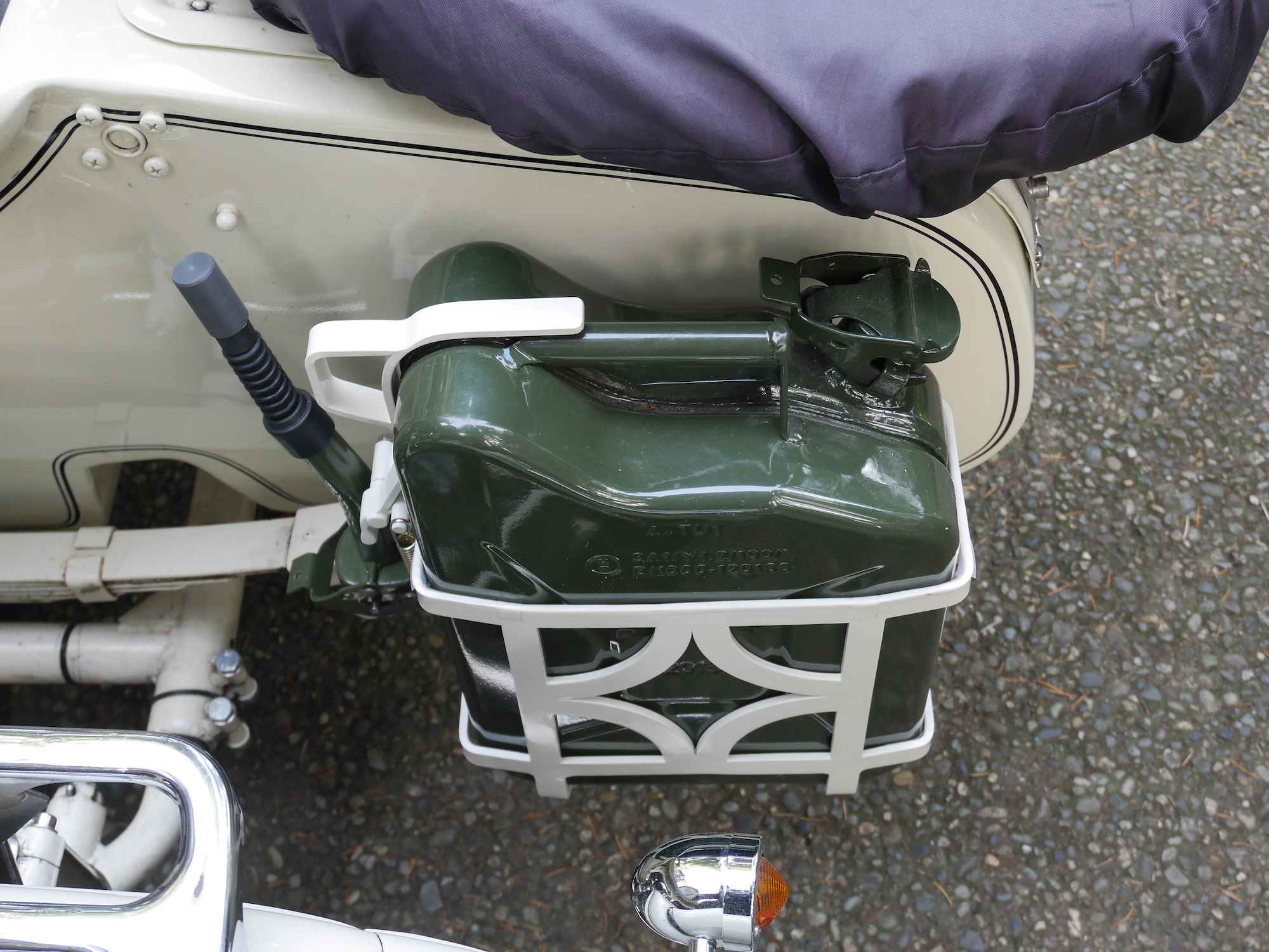
Projekt Benzinkanisterhalter, Teil 2, das Zusammenbauen:
Alle Teile werden jetzt zusammengeschweißt. Die Rundbögen sind von einem Kranz aus einer Bremse, die in 4 Teile geschnitten worden ist:
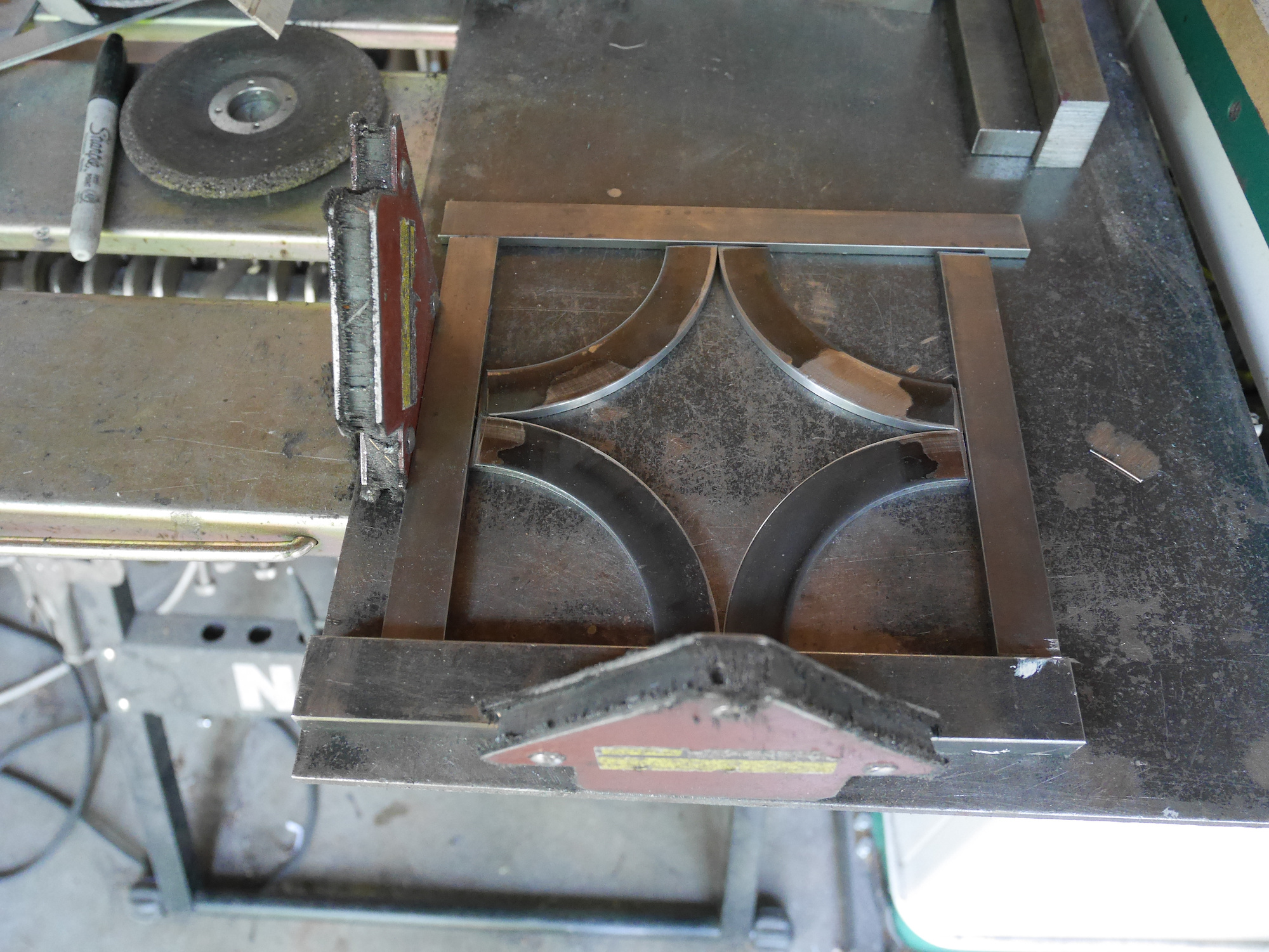
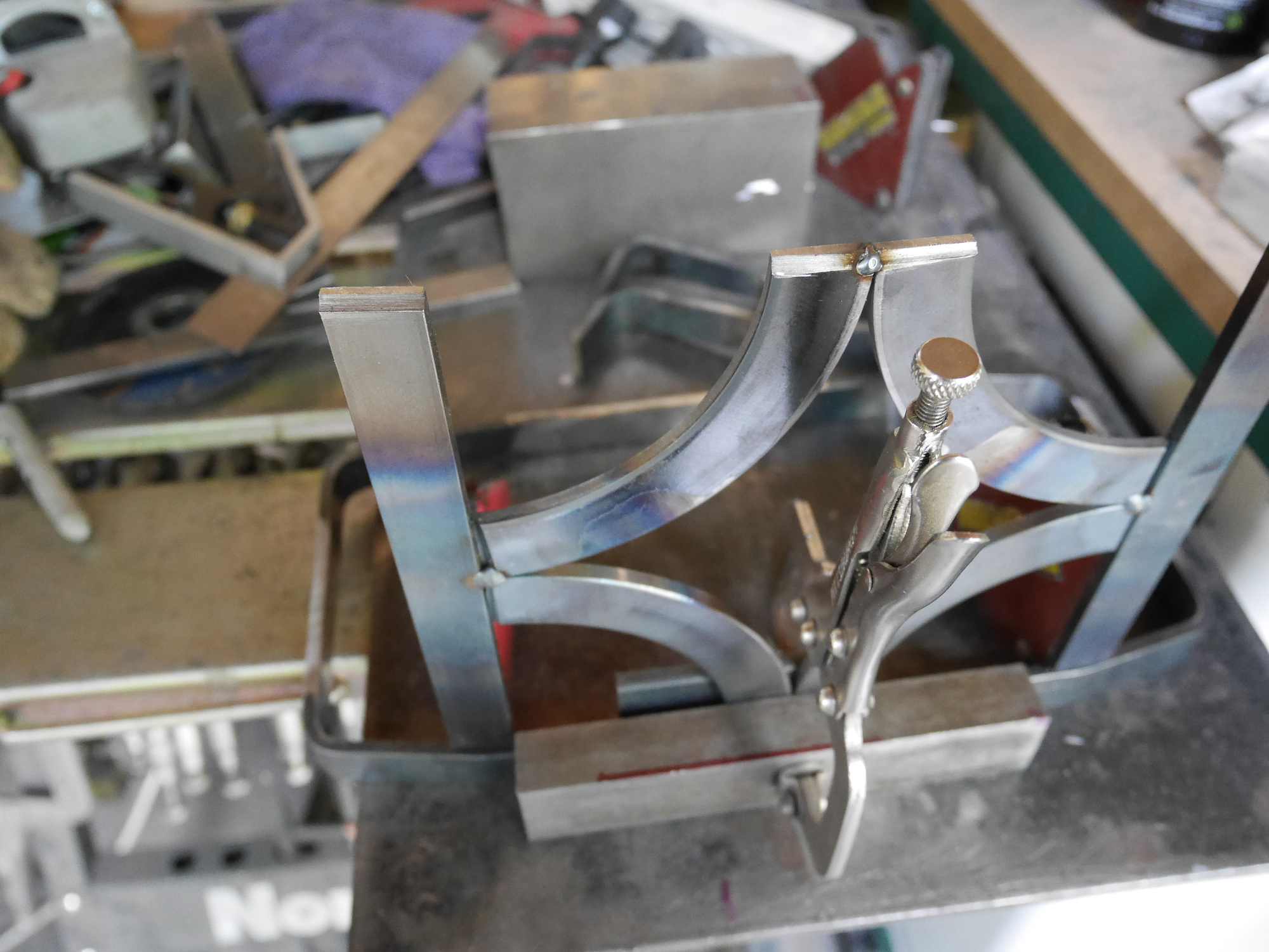

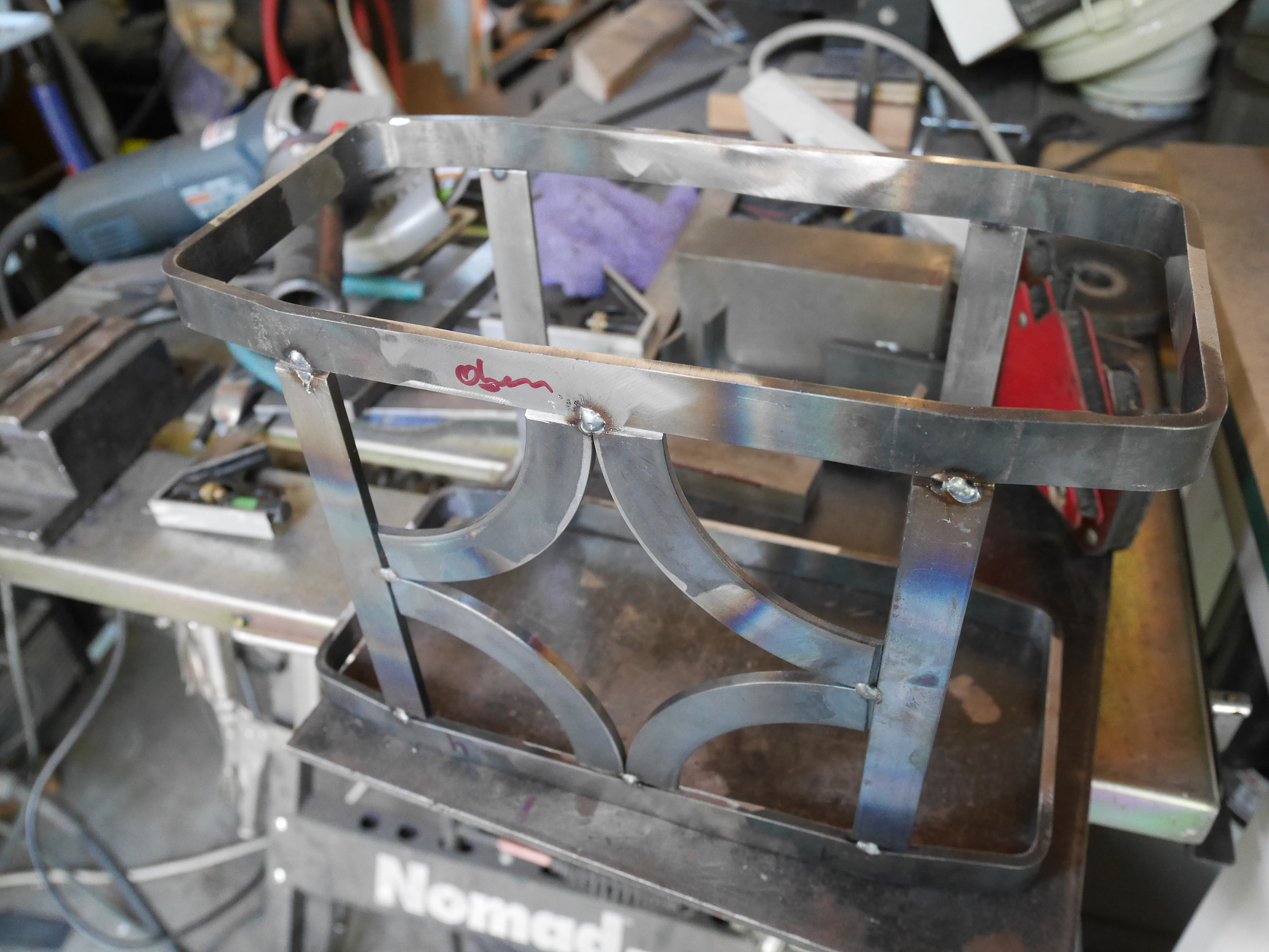
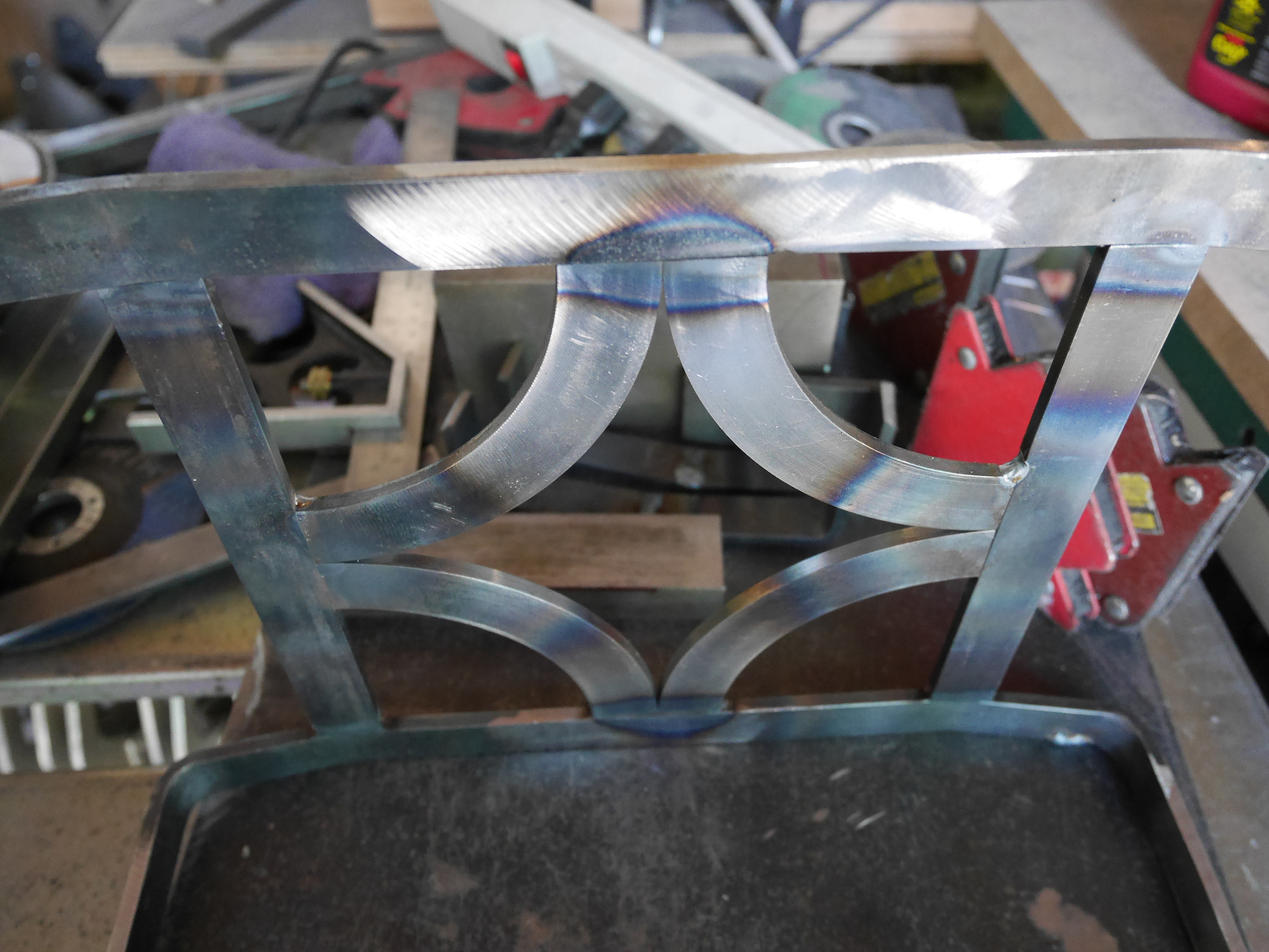

Die Halterung wird mit einem Halter befestigt, der an die Innenseite des Beiwagens angepasst ist:
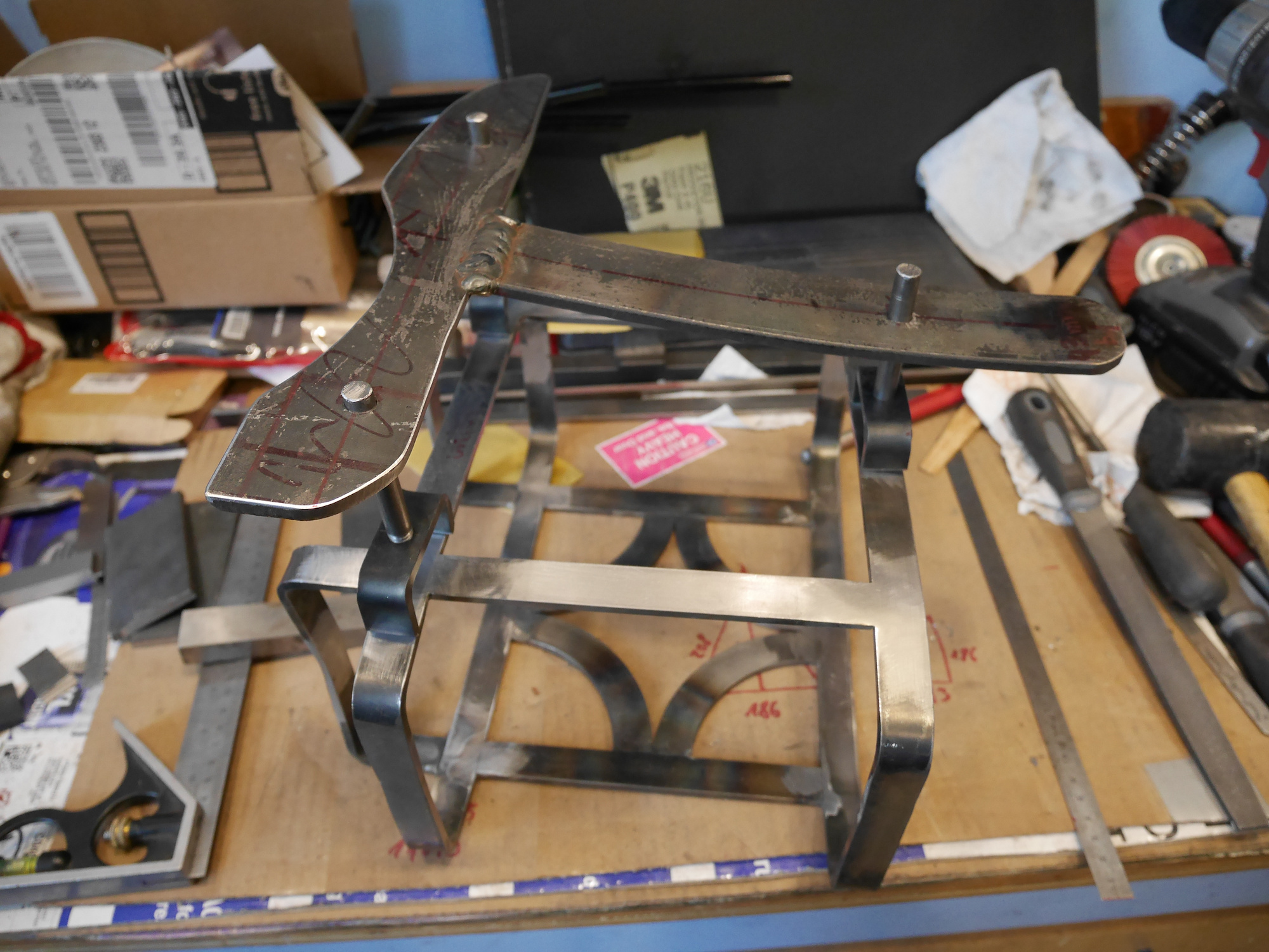